Expert Tips for Maximizing Heavy Equipment Efficiency
Meta Description: Learn expert tips to maximize heavy equipment efficiency and productivity rates at construction sites through operator training, maintenance, and technology.
To maximize productivity and efficiency at construction sites, it’s essential to manage intricate and complex machines carefully.
You can achieve maximum productivity by training operators, tracking equipment health, automating repetitive tasks, and maintaining machines.
Properly utilizing each piece of equipment by matching it to the right job results in higher quality work, lower hourly costs and rental fees, and increased productivity across multiple projects and job sites.
Being aware of general costs and productivity levels lets you do the job with fewer passes and the right machines.
Key Takeaways
- Standardizing the fleet and equipment selection can lead to improved efficiency and cost-effectiveness.
- Optimizing equipment utilization through strategic scheduling and task prioritization can help maximize productivity.
- Following preventative maintenance best practices, including routine inspections and adhering to maintenance schedules, can reduce downtime and extend equipment lifespan.
- Investing in operator training programs and incentivizing safe and efficient practices can enhance operator skills and boost overall equipment performance.
Invest in a Standardized Fleet
When you standardize your fleet, you streamline maintenance and operation across the board.
This move simplifies training for your crew and lowers the costs of keeping multiple types of machinery running.
Simplifies Maintenance and Operation
Investing in a standardized fleet can significantly streamline maintenance and operation, making managing equipment across various projects easier. By doing so, you’ll unlock a host of benefits:
- Enhanced Preventive Maintenance: With similar machinery, you can establish a consistent schedule and keep better maintenance records, reducing downtime.
- Simplified Training for Safe Operation: Operators can seamlessly transition between machines, ensuring proper operation without extensive retraining.
- Streamlined Inventory Management: Spare parts and service items can be standardized, simplifying procurement and storage.
Lowers Long-Term Costs
Beyond simplifying maintenance and operation, standardizing your fleet reduces long-term expenses by eliminating the complexity of managing multiple equipment types. When investing in a standardized fleet, you’re not just streamlining your operations but actively reducing operating costs.
Fewer unique parts mean less inventory to manage. You’ll save on equipment depreciation, as standardized assets tend to hold their value better when upgrading.
With consistent maintenance plans, you can minimize downtime, ensuring all your machines are ready when needed. This approach makes it easier to cross-train your operators, further enhancing efficiency.
In short, a standardized fleet isn’t just a convenience—it’s a strategic move to gain control over your financial future in the heavy equipment industry.
Choose the Right Equipment for Each Job
When picking out heavy equipment for a job, it’s crucial to weigh the size, power, and capabilities against the task at hand.
You’ll need to decide whether buying or renting is the most cost-effective choice, considering your project’s duration and equipment use frequency.
Always ensure the machinery you select meets the job’s demands without compromising efficiency or safety.
Consider Size, Power, and Capabilities
Select heavy equipment that aligns with the specific size, power, and capabilities required for the tasks to maximize your project’s efficiency. Choosing the right equipment isn’t just practical—it’s vital for controlling the job’s outcome.
Here’s what to consider:
- Match Machine Size: Avoid the extra cost and inefficiency of oversized equipment that can hinder productivity and site logistics.
- Power Requirements: Ensure the machinery’s power matches the job’s demands to prevent underperformance or unnecessary fuel consumption.
- Capabilities and Control Systems: Leverage machine control systems to enhance precision, and always deploy skilled operators who can maximize the potential of your equipment.
Buy vs Rent Decision
You’ll often face the critical decision of buying or renting heavy equipment. This choice hinges on the frequency of use and the financial implications for your project. Evaluate how often you’ll need the equipment. Renting equipment may be more cost-effective if it’s for a one-off job or infrequent tasks. Conversely, if the gear is essential for daily operations, investing in certified used equipment or new equipment could save money in the long run.
Consider each project’s unique requirements—owning offers flexibility, while renting can be easier on cash flow. Assess the project’s duration and complexity; short-term, complex jobs might warrant rentals for optimal efficiency. Always seek professional advice to weigh the pros and cons, ensuring you make a controlled, informed choice.
Optimize Equipment Utilization
You’ll need to schedule jobs and crews strategically to maximize the efficiency of your heavy equipment.
Keep a close eye on machine hours and downtime to pinpoint where you can cut back on wasted time.
Schedule Jobs and Crews Strategically
How can you ensure every piece of heavy equipment is used to its fullest potential? Start by strategically scheduling jobs and crews to minimize downtime and optimize utilization. Here’s what you need to do:
- Align Project Timelines: Coordinate the availability of your heavy equipment with project time constraints, ensuring you’re not left with idle machinery.
- Capitalize on Crew Capacity: Match equipment operator schedules to peak job site productivity periods so your team always drives value.
- Prioritize Tasks Smartly: Focus on high-impact, time-sensitive tasks first, maximizing the return on every minute of operating heavy equipment.
Track Machine Hours and Downtime
Monitoring machine hours and downtime meticulously can significantly enhance equipment utilization and maintenance scheduling. By tracking operating hours, you’re equipping yourself with the data to pinpoint when maintenance is due, preemptively tackling issues before they balloon into costly repairs. Keep a close eye on your monitor operating records to detect irregularities that could signal an underlying problem.
Furthermore, log every instance of non-productive time. This isn’t just about recording but analyzing patterns and root causes. By doing so, you’re setting the stage for reducing downtime. Utilize these inevitable pauses in operation for necessary training, inspections, and repairs.
Through continuous process improvement, you’ll curb downtime and boost the productivity of your heavy equipment, ensuring you’re in full control of your operational efficiency.
Follow Preventative Maintenance Best Practices
You’ve got your heavy equipment out on the job, but preventative maintenance is key to keeping it running smoothly.
Make it a habit to perform routine inspections and services; this step can save you from unexpected breakdowns and costly repairs.
Don’t forget to keep detailed maintenance logs, as they’re crucial for tracking your equipment’s health and scheduling future upkeep.
Perform Routine Inspections and Services
To maximize the longevity and efficiency of your heavy equipment, it’s essential to conduct regular inspections and adhere to the manufacturer’s recommended maintenance schedule. The health of your machines is in your hands, and with the right inspection and preparation time, you can avoid the stress of unexpected downtime.
Ensure they’re functioning properly by implementing these steps:
- Dedicate specific intervals for safety checks to identify potential hazards or malfunctions.
- Keep an accurate log of all services performed, fostering transparency and accountability.
- Empower your team with training on maintenance best practices, enhancing their ability to detect and remedy issues.
Keep Detailed Maintenance Logs
Building on the foundation of routine inspections and services, keeping detailed maintenance logs is critical to ensure your heavy equipment receives timely and consistent care. These logs are your roadmap to repairing intricate issues and safeguarding equipment operations before they escalate. Adhering to the manufacturer’s recommended maintenance schedule is key, and documenting every task, from oil changes to filter replacements, builds a comprehensive history.
Your maintenance logs are a powerful tool. They allow you to identify patterns, which can forecast potential problems and guide your decision-making. By meticulously recording maintenance and repairs, you’re not just following best practices but taking command of your heavy equipment’s health and efficiency.
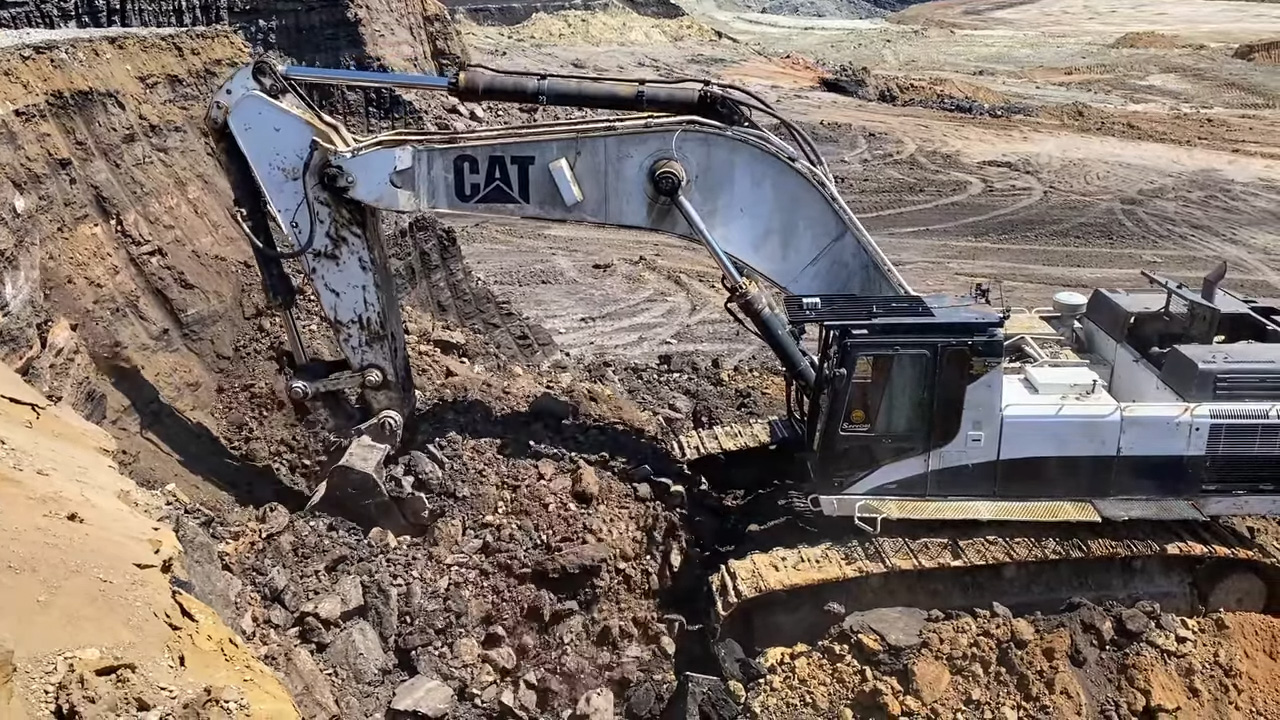
Hire Skilled and Trained Operators
You know your heavy equipment has the potential to boost productivity. Still, it’s only as effective as the person operating it. Investing in training programs ensures your operators have the skills to use machinery safely and at full capacity.
Incentivize their performance to encourage a workplace where safety and efficiency are top priorities, leading to better results and fewer setbacks.
Invest in Operator Training Programs
Investing in a robust operator training program can significantly enhance the efficiency and safety of heavy equipment operations.
Here’s what you’ll gain:
- Improved operator skill: Well-trained equipment operators handle machines precisely, reducing the risk of costly mistakes.
- Enhanced safety: A focus on safety training means fewer accidents and a secure environment for your team.
- Increased productivity: Experienced operators know how to maximize equipment potential, directly boosting your project’s output.
Incentivize Safe and Efficient Operations
To maximize heavy equipment efficiency, it’s crucial to hire skilled operators and provide incentives for safe and efficient practices.
By offering comprehensive training programs, you can ensure that every machine operator is equipped to handle safety issues and operate with higher productivity. But training alone isn’t enough.
You need to implement incentive programs that recognize and reward those who consistently show excellence in their operating records. Regularly updating these programs with industry best practices and technological advancements keeps your team at the forefront of operational efficiency.
Encourage feedback and open communication; this empowers operators to continuously improve their skills and operations to remain efficient and safe.
Leverage Telematics and Data Analytics
You can maximize your heavy equipment’s efficiency by closely monitoring machine performance and health through telematics.
Identifying issues early will prevent costly downtime and ensure your equipment is always running at peak performance.
Plus, with the hard data, you can quantify the return on your investment, ensuring every dollar spent is a step towards greater efficiency.
Monitor Machine Performance and Health
Harness the power of telematics and data analytics to closely monitor and enhance the performance and health of your heavy equipment. By leveraging machine data gathering technology, you’re not just keeping an eye on your equipment but taking command of its potential.
Here’s how you can tap into this potential:
- Optimize Productivity: Utilize equipment data to pinpoint inefficiencies and streamline operations.
- Prevent Downtime: Analyze equipment technology to predict and prevent costly breakdowns.
- Control Costs: Monitor fuel consumption and machine utilization to reduce expenses.
This approach transforms raw machine data into actionable insights, giving you the power to make informed decisions.
Stay ahead of the curve by integrating equipment technology into your maintenance strategy, ensuring your fleet operates at peak efficiency.
Identify Issues Early and Quantify ROI
Leveraging telematics and data analytics allows you to detect potential equipment issues early and accurately measure your return on investment. You’re equipped to make informed decisions that directly affect productivity by tracking performance, fuel usage, and maintenance needs. These tools offer a clear picture of your heavy equipment’s operational health, enabling you to pinpoint inefficiencies that might otherwise go unnoticed.
Understanding the data helps you optimize equipment productivity, ensuring your machines work as hard as you do. When you identify issues early, you’re not just saving on repair costs but also maintaining peak production rates. Use this insight to decide strategically on maintenance, replacement, or operational adjustments, and watch as your ROI reflects the benefits of a well-oiled, data-driven approach.
Continuously Improve Policies and Procedures
You must listen to those on the front lines to keep your heavy equipment running at peak efficiency. Regularly seek out and act on operator feedback to refine your procedures, ensuring they’re both compliant and practical.
Evaluate and adjust your processes consistently so you’re always a step ahead in productivity and safety.
Encourage Operator Feedback
Valuing operator feedback can significantly streamline the continuous improvement of policies and procedures, directly impacting the efficiency and safety of heavy equipment operations. As you’re operating heavy machinery, your insights are vital. Here’s how to take control:
- Open Communication: Establish channels where your voice is heard, ensuring the job site is a place of collaborative progress.
- Policy Evolution: Play a pivotal role in policy updates that affect your daily tasks and overall construction equipment productivity.
- Innovation Encouragement: Suggest practical improvements that can make a measurable difference.
Regularly Evaluate and Adjust Processes
As you refine operations, regularly evaluating and adjusting processes is key to driving the efficiency of your heavy equipment. By implementing a system to track and analyze equipment productivity data, you’ll pinpoint where improvements can be made. Adapting and refining your methods based on these performance metrics and construction equipment productivity norms is crucial. This way, you’re not just keeping pace but setting the standard.
To further enhance efficiency, consider automating repetitive tasks. This shaves off production time and allows your team to focus on more complex issues. Don’t forget to continuously improve policies and procedures, aiming for the next level in improving productivity. And remember, soliciting feedback from those on the ground is invaluable for making practical adjustments.