Equipment Rental Maintenance Checklist
Meta Description: Regular inspections and maintenance with a comprehensive checklist control equipment condition, optimize safety, and reduce unexpected repairs for rental companies.
Rental companies should regularly inspect their equipment following the manufacturer’s guidelines. This prevents potential issues and maintains reliable, safe equipment for customers. Managers can use maintenance checklists to methodically examine equipment parts and functionality. Addressing defects quickly optimizes equipment conditions and avoids costly repairs. Thorough inspections and timely maintenance are key for heavy equipment rental businesses to control operations.
Key Takeaways
- Regular equipment maintenance reduces downtime and ensures safety.
- Thorough inspections help identify potential defects before they escalate.
- Cleaning and sanitizing equipment uphold hygiene standards.
- Adhering to manufacturer guidelines extends the lifespan of rental equipment and maintains a reputation for reliability.
Rental Equipment Maintenance Checklist
Start by examining the exterior condition of your rental equipment for any signs of wear or damage.
Next, check the interior condition to ensure everything is clean and in proper working order.
Lastly, verify the functionality, fluids filters, and safety components to guarantee the equipment is reliable and safe for use.
Exterior Condition
How can you ensure your rental equipment’s exterior is in top shape?
Start by checking the tire condition for safety and operability. Look for adequate tread depth and any signs of damage. Remove foreign objects that could jeopardize safety.
A visual inspection of vehicle lights is critical; confirm that headlights, taillights, turn signals, and brake lights function correctly for visibility and to avoid safety concerns.
Examine the undercarriage to catch leaks or damage from debris, maintaining the integrity of your well-maintained equipment.
For hydraulic systems, check for leaks and hose condition.
Don’t forget a thorough engine review, including oil level and air filter, to ensure your clean equipment performs safely and efficiently.
Interior Condition
After ensuring the exterior of your rental equipment is in optimal condition, shift your attention to the interior to maintain a safe and comfortable operating environment. Start with a thorough inspection checklist.
Check the HVAC system for functionality; it’s essential for operator comfort and safety. Ensure air filters are clean to prevent dust and particulates from circulating inside the cabin.
Test all controls and gauges to confirm they’re in working order. Don’t overlook the importance of checking for any signs of wear and tear on the seats and safety belts. Any interior damage or malfunction can affect the operator’s ability to control the equipment safely.
Functionality
To ensure your rental equipment operates smoothly, routinely verify its functionality as part of your maintenance checklist. Preventative maintenance keeps your gear working properly and minimizes equipment downtime.
Here’s what you need to inspect:
Basic Inspection
- Check for any visible damage or wear.
- Ensure all controls are responsive.
Specific Checks
- Engine Inspection: Examine oil levels, spark plugs, and air filters.
- Safety Features: Confirm that the safety equipment in the cab is present and functional.
Fluids and Filters
Ensuring your rental equipment’s fluids and filters are properly maintained is crucial for optimal performance and longevity. You’ve got to check fluid levels regularly, including engine oil, coolant, and hydraulic fluid, to keep things running smoothly. Don’t forget to inspect and swap out filters as necessary.
Your air, oil, and fuel filters are your first line of defense against contaminants. Adhere to the manufacturer’s instructions on when to replace these critical components.
Keep an eye on the fuel system for leaks or damage, and monitor the transmission fluid’s condition, replacing it if needed. Remember, maintaining hydraulic filters is one of your key maintenance responsibilities.
It’s not just about keeping your equipment in top shape—it’s about taking control of your machinery’s health.
Safety Components
Regularly inspecting safety components like tires, lights, and the undercarriage is key to keeping your rental equipment safe and fully operational. Your proactive approach to safety equipment inspection ensures working conditions and wards off emergency repairs.
Verify Tires and Lights
- Check for adequate tread depth and tire pressure.
- Ensure lights are functioning correctly for visibility.
Inspect Undercarriage and Hydraulics
- Look for signs of wear or damage.
- Confirm hydraulic systems are leak-free and responsive.
Electronics
Before operating your rental equipment, it’s essential to thoroughly check the electronics to prevent malfunctions and maintain optimal performance. Inspect each electronic component for signs of wear or damage, ensuring all connections are secure and intact.
Testing the equipment under actual working conditions includes electrical, mechanical, and safety checks. Make sure all electronic parts are functioning correctly. If there’s a malfunction, provide a detailed description to avoid hefty repair costs later.
Regular maintenance and servicing are your best defenses against unexpected downtime. Don’t forget to clean electronic interfaces, connectors, and internal components. By taking these steps, you’ll ensure your equipment remains reliable, safe, and ready for the job.
Essential Components of a Rental Maintenance Checklist
Before renting out equipment again, ensure it’s up to the task with a comprehensive maintenance checklist.
Start with a visual inspection for any obvious damage, followed by functionality tests to ensure everything operates as it should.
Don’t overlook the importance of routine cleaning and maintenance, and address any repairs immediately to keep your gear in top condition.
Visual Inspection
To ensure your rental equipment remains in prime condition, begin with a thorough visual inspection, targeting areas most susceptible to wear and potential damage. Here’s what you should focus on:
Inspecting for Wear and Damage
- Check for cracks, dents, or corrosion.
- Look for signs of excessive wear on moving parts.
Identifying Safety Hazards
- Ensure there are no faulty wirings or loose components.
- Verify that all safety guards are in place and intact.
As you maintain your rental equipment, don’t overlook the importance of removing any debris that could hinder performance or cause damage.
Functionality Tests
Having completed a visual inspection of your rental equipment, performing functionality tests to confirm that all vital components operate correctly is crucial. These tests are a key part of your maintenance checklist and are vital to your rental business. When renting equipment, ensuring its fully operational condition safeguards your reputation and customer productivity.
Check each piece of equipment methodically—start the engine, operate the controls, and verify that all features perform as expected. This step pinpoints any malfunctions and helps prevent potential breakdowns during use. Regular functionality tests are non-negotiable; they contribute to the safety, reliability, and control that your clients expect when they choose your service.
It’s your proactive approach to maintenance that sets you apart.
Cleaning and Maintenance
After thorough functionality tests, ensure your equipment’s longevity and peak performance by implementing a rigorous cleaning and maintenance routine. This is crucial to reducing downtime and ensuring safety.
Here’s what you need to focus on:
Cleaning
- Remove debris and dirt from common areas where grime accumulates, preventing malfunctions.
- Sanitize control panels and touchpoints to uphold hygiene standards.
Maintenance Work
- Inspect and replace worn-out parts to maintain operational integrity.
- Lubricate moving components to prevent wear and tear.
Repairs
Ensure you promptly address any identified issues by repairing or replacing faulty components as part of your regular equipment maintenance routine.
Regular, thorough inspections allow you to pinpoint potential defects before they escalate into costly repairs.
When you test equipment under operational conditions, you’re ensuring its performance, safety, and good condition.
Keeping your equipment clean is equally vital, as it can prevent many issues from arising.
Always update the equipment’s status in your rental software system to keep track of necessary repairs.
This proactive approach to maintenance ensures your rental equipment remains reliable for your customers. It helps you maintain control over your maintenance expenses.
Developing a Rental Equipment Maintenance Checklist
To create an effective rental equipment maintenance checklist, start by involving your team, particularly those who work closely with the equipment.
Ensure you’re consulting the manufacturer’s guidelines to address specific maintenance requirements.
Lastly, consider the type and frequency of use for each piece of equipment, as this will influence the maintenance tasks you include on your checklist.
Involve Relevant Staff
Gather your team of technicians and operators to kick off the development of a comprehensive rental equipment maintenance checklist. You know these folks understand the daily grind and can pinpoint the routine tasks to keep your gear running smoothly.
Technicians
- Inspection Expertise: Identify critical points prone to wear and tear. Suggest preventive measures for common issues.
- Tool Mastery: Recommend the right tools for each maintenance task. Demonstrate proper use to avoid mishaps.
Operators
- Daily Use Insights: Share experiences on equipment stress points. Help tailor the checklist to real-world conditions.
- Efficiency Ideas: Offer tips to streamline maintenance procedures. Highlight time-saving practices for routine checks.
Involve your staff; they’re your eyes and ears on the ground, ensuring your equipment maintenance checklist isn’t just thorough but practical.
Review Manufacturer Guidelines
Delving into the manufacturer’s guidelines is crucial, as it provides the blueprint for maintaining each type of rental equipment according to precise standards. These guidelines are your ace in the hole for grasping the specific maintenance needs and timelines that the manufacturer recommends. By adhering to these instructions, not only do you ensure that the machine operates at peak performance, but you also safeguard its warranty.
Incorporating manufacturer guidelines into your checklist is a non-negotiable. It’s the smart way to align your repair protocols with the expectations of those who created the machinery. This due diligence translates into longer life spans for your rental fleet and bolsters your reputation for providing reliable, well-maintained equipment.
Consider Equipment Type and Use
Building on the foundation of manufacturer guidelines, it’s vital to tailor your maintenance checklist to the specific types of equipment and their intended uses. Your maintenance checklist should address the unique demands of each equipment type and how it’s used, ensuring longevity and reliability. Here’s how you can consider specific needs:
Frequency of Inspections
- High-use equipment: Increase inspection regularity to prevent wear-and-tear issues.
- Seasonal tools: Schedule inspections post-season and before peak usage.
Key Inspection Areas
- Heavy machinery: Prioritize undercarriage, hydraulics, and engine checks.
- Vehicles: Focus on tire condition, lights, and cab integrity.
Adapt your approach to your equipment’s use and specific needs, maintaining control over your rental inventory’s condition and performance.
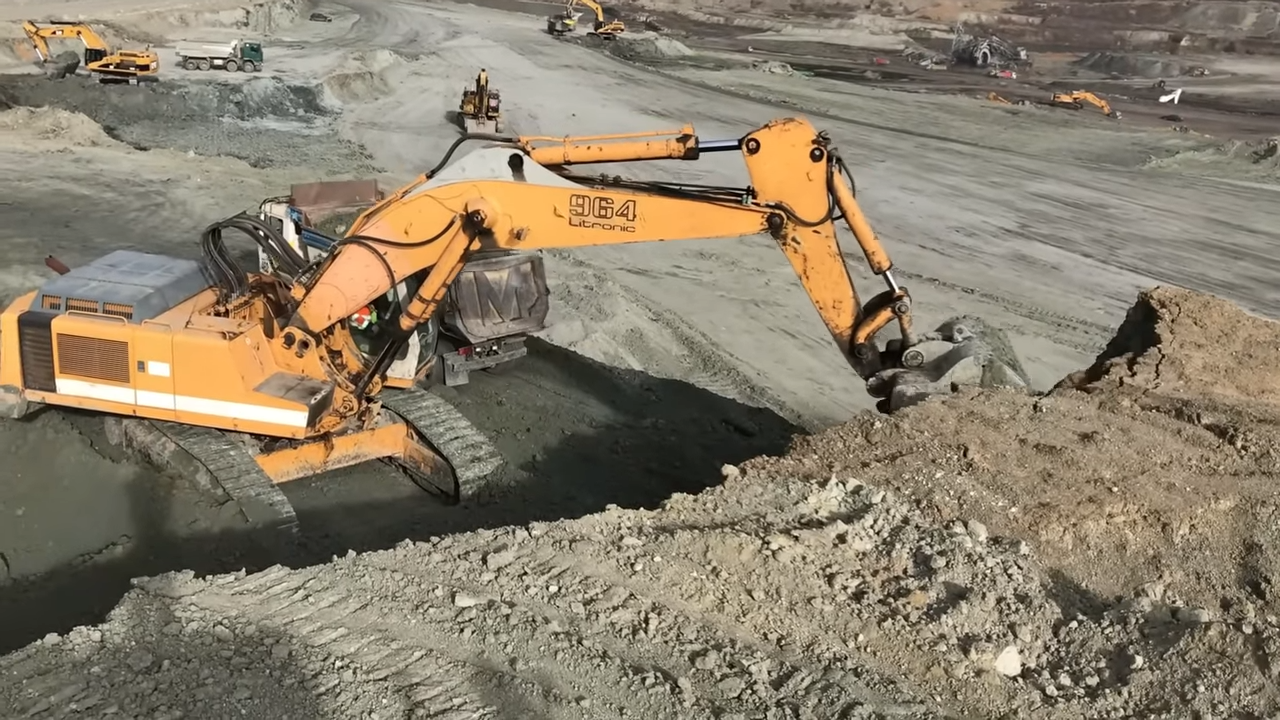
Benefits of a Rental Maintenance Checklist
By adopting a rental maintenance checklist, you’re not just ticking boxes; you’re significantly enhancing the safety of your equipment.
This proactive measure extends the life of your assets and elevates the service you provide to customers.
Plus, it’s a surefire way to cut unexpected repairs and downtime costs.
Improved Safety
As directed by a rental maintenance checklist, regular maintenance, and thorough inspections significantly enhance safety for equipment operators and nearby personnel. By sticking to a well-defined checklist, you’re not just ticking boxes but actively preventing mishaps and ensuring a safe work environment.
Here’s how:
Prevent Accidents
- Identifies potential defects
- Ensures equipment operates safely
Reduce Hazards
- Keeps smoke alarms functional
- Maintains air conditioning to prevent overheating
- Secures windows and other structures from damage
- Clears away other debris that could cause injury
Increased Equipment Lifespan
Implementing a rental maintenance checklist can significantly extend the life of your equipment, ensuring it remains functional and reliable for longer periods. Adhering to a landlord maintenance checklist keeps your rental property’s equipment in top shape, staving off the wear and tear that can lead to premature failure. This proactive approach doesn’t just save money on costly emergency repairs; it also means you’re less likely to face the expense of replacing equipment before its time.
In the long run, a well-maintained inventory translates to operational efficiency and uninterrupted service, which is crucial for retaining tenants and maintaining a positive reputation. Take control of your equipment’s destiny—regular maintenance isn’t just a recommendation; it’s an investment in the longevity of your rental business.
Enhanced Customer Service
Ensuring your equipment is meticulously maintained with a checklist not only streamlines your operations but also elevates the service experience for your customers. Here’s how:
- Avoid misunderstandings: Ensures customers and tenants are on the same page.
- Saves money: Prevents unexpected costs for both parties.
- Thorough inspections: Keeps equipment in top condition, enhancing customer satisfaction.
- Engine checks: Guarantees reliability, so tenants and property managers trust your service.
Utilizing equipment rental software like Quipli’s integrates inventory and scheduling, offering you control and your customers seamless service.
Reduced Costs
A well-executed maintenance checklist slashes costs by nipping potential equipment failures before they balloon into pricier problems. By adhering to a rental maintenance checklist, you’re taking a proactive approach to equipment care. This vigilance ensures that you catch issues early on, which translates to reduced costs from avoiding large-scale repairs.
Regular inspections and timely interventions keep your rental equipment in optimal condition, staving off the need for expensive replacements. Investing a little in routine maintenance now can save you a lot, keeping your budget in check and your rental operations running smoothly.
Inspection Process and Procedures
Establishing a clear inspection process is vital to maintain the reliability of your rental equipment.
Begin by assigning responsibilities to ensure each piece of equipment undergoes a thorough check; then, set a regular schedule that aligns with usage patterns and maintenance needs.
Conduct a detailed review of all parts during the inspection, perform necessary repairs or replacements, and meticulously record every detail for future reference.
Assign Responsibilities
Define clear roles and responsibilities for team members involved in the inspection process to guarantee efficiency and accountability.
In the rental industry, the equipment maintenance checklist is a pivotal tool that ensures your assets remain in top condition, adhering to the lease agreement standards.
When you assign responsibilities, consider the following:
- Inspector: Conducts thorough checks and reports issues.
- Maintenance Coordinator: Schedules repairs and confirms completion.
- Oversight Team: Reviews inspection outcomes and enforces lease agreement compliance.
- Quality Assurance: Monitors the consistency and thoroughness of inspections.
Regular updates to these roles are critical to adapting to the evolving demands of your rental business.
Ensure everyone understands their tasks and the importance of their role in maintaining the value and safety of your equipment.
Set Schedule
Having assigned specific roles to team members, it’s crucial to establish a regular schedule for equipment inspections that aligns with the responsibilities and ensures consistent upkeep. Your set schedule should reflect a systematic approach, considering how often each piece of rental equipment is used and the length of rental periods.
Define clear processes and procedures that standardize maintenance evaluations, ensuring your team knows exactly what to look for during each inspection. This structured approach lets you proactively pinpoint and resolve maintenance issues, minimizing the risk of unexpected and costly repairs.
Conduct Thorough Inspection
Ensure you thoroughly inspect the rental equipment before its next use to prevent breakdowns and avoid expensive repairs. Here’s how to assess such equipment effectively:
- Before each rental: Guarantee functionality and safety.
- Weekly: If daily isn’t feasible, especially for high-use items.
Check specific components:
- Tire Condition: Look for wear and proper inflation.
- Vehicle Lights & Hydraulics: Ensure operational integrity.
- Undercarriage: Examine for damage or excessive wear.
Adhere to the manufacturer’s service manual for detailed inspection procedures and record all findings meticulously. Remember to perform partial inspections regularly for long-term rentals to maintain ongoing functionality.
Make Repairs and Replace Parts
Following your comprehensive inspection, promptly address any identified defects by repairing or replacing parts to maintain the equipment’s optimal performance and safety. Test the equipment under operational conditions and tackle issues immediately. Take action if you find malfunctioning electrical, mechanical, or hydraulic components. Ensure all moving parts and connections work flawlessly to avoid any operational hiccups.
For vehicles with hydraulic equipment, conduct an engine examination. Check the oil level, spark plugs, and air filter, and verify that the cab’s safety equipment is functional. Regular care and preventative maintenance are your best strategies to keep the equipment reliable, minimize downtime, and sidestep expensive repairs.
Record Details
To create a reliable maintenance history, document every detail of your equipment’s inspection process, noting the date, inspector’s name, and any specific observations. Your rental business depends on the integrity of your equipment, and meticulous record-keeping is crucial.