Heavy Equipment Inspection Best Practices for Safety and Efficiency
Meta Description: Learn the best practices for heavy equipment inspection to maintain safety and operational efficiency. Follow official guidelines and use comprehensive checklists for thorough examinations.
Regular inspections are crucial to maintain heavy equipment safety and efficiency. Following manufacturer recommendations and regulatory requirements ensures proper maintenance, optimal performance, and legal compliance. Thoroughly examining critical components using comprehensive checklists enhances the inspection process. Promptly addressing issues prevents escalation. Incorporating technology like sensors improves efficiency. This article explores best practices for heavy equipment inspection.
Key Takeaways
- Regular heavy equipment inspections are crucial for maintaining safety and operational efficiency on work sites.
- Following official guidelines and checklists, including manufacturer recommendations and regulatory requirements, is essential for effective inspections.
- Adhering to manufacturer recommendations helps prevent accidents, ensures optimal equipment performance, and facilitates efficient maintenance through maintenance software and detailed checklists.
- Compliance with regulatory requirements, such as OSHA guidelines, helps ensure occupational safety, upholds stringent safety protocols, and avoids hefty fines. Comprehensive inspection checklists further enhance safety and operational efficiency by facilitating thorough visual examinations and streamlining the inspection process.
Overview of Heavy Equipment Inspection Importance
Regular heavy equipment inspections are a vital practice that significantly enhances safety and operational efficiency on work sites.
The inspection process identifies potential safety hazards and prevents equipment failures.
By committing to regular inspections, operators ensure compliance with legal standards and foster a culture of conscientious maintenance.
This proactive approach is crucial in maintaining a reliable and secure work environment.
Follow Official Guidelines and Checklists
Adherence to the manufacturer’s recommendations is fundamental for heavy equipment’s proper maintenance and longevity.
Complying with all regulatory requirements is equally critical to ensure safety and legal operation.
Utilizing comprehensive inspection checklists can significantly enhance the effectiveness and thoroughness of the inspection process.
Adhere to Manufacturer Recommendations
Ensuring the safety and efficiency of heavy equipment begins with strict observance of the manufacturer’s official guidelines and inspection checklists.
- Adhering to inspection frequency as prescribed
- Prevents accidents
- Ensures optimal performance
Utilizing maintenance software aligns with manufacturers’ recommendations.
- Tracks specific equipment needs
- Efficiently schedule maintenance
Following detailed checklists ensures every aspect of equipment care is addressed, maintaining a close bond of trust and reliability with the machinery.
Comply with Regulatory Requirements
Building upon the foundation of manufacturer recommendations, conducting heavy equipment inspections following official regulatory requirements is equally critical to maintaining a safe and legally compliant operation.
Following OSHA guidelines and local mandates ensures occupational safety and upholds stringent safety protocols.
Neglecting these inspection requirements risks hazards and may lead to hefty fines, emphasizing the need for diligent compliance.
Use Comprehensive Inspection Checklists
To guarantee a meticulous and effective inspection process for heavy equipment, it is essential to utilize comprehensive checklists that align with official guidelines and standards.
Benefits of a Comprehensive Checklist:
- Ensures adherence to OSHA and manufacturer guidelines
- Facilitates a thorough visual examination
- Streamlines the process of conducting inspections
Regularly update the heavy equipment inspection checklist to reflect the latest safety and operational standards.
Inspect All Critical Components Thoroughly
A comprehensive examination of heavy equipment’s critical components is vital to ensure operational safety and longevity.
This includes checking the structural integrity for any signs of stress or damage, closely examining operational systems such as the engine and hydraulics for performance issues, and assessing fluid levels and quality to prevent mechanical failures.
Special attention should be given to high-wear parts, as these are more likely to compromise the equipment’s functionality and safety if not properly maintained.
Check Structural Integrity
Ensuring the structural integrity and operational safety of heavy equipment begins with thoroughly inspecting all critical components, including the engine, hydraulics, electrical systems, brakes, and tires.
Utilize comprehensive inspection checklists to:
- Identify potential hazards
- Ensure safety by detecting signs of wear or damage
- Guide regular inspection processes for consistency and thoroughness
Regularly updating checklists according to industry standards is key to maintaining structural integrity.
Examine Operational Systems
Conducting a meticulous examination of all critical components is the cornerstone of operational system inspections in heavy equipment maintenance. Equipment inspections must prioritize engines, cooling systems, hydraulic systems, and electrical components.
Carefully check for loose connections and signs of wear. A detailed checklist, reflective of industry standards, ensures a comprehensive review of these vital parts, enhancing safety and efficiency in your heavy machinery’s performance.
Assess Fluid Levels and Quality
Regular inspection of fluid levels and quality is a fundamental aspect of maintaining the health and efficiency of heavy equipment. Adhering to these checks can prevent costly downtime:
- Ensure all fluid levels fall within recommended ranges
- Check for oil leaks; address promptly
- Assess air filters for contamination
Regular equipment inspections safeguard against breakdowns. Following the manufacturer’s guidelines is key to heavy equipment maintenance.
Focus on High-Wear Parts
Building on the foundation of monitoring fluid levels and quality, a meticulous examination of high-wear parts is equally crucial for maintaining the operational integrity of heavy equipment.
Thoroughly inspect heavy equipment, focusing on engines, hydraulics, and tires to prevent equipment breakdowns.
Prioritize elements that impact safety and costs, documenting findings to avert premature wear and accidents, thereby ensuring efficient equipment maintenance.
Document Inspection Findings in Detail
Accurate documentation is crucial in the heavy equipment inspection process, providing a reliable account of the equipment’s condition.
It is imperative to note the exact location of any issues found and supplement the written record with photos or videos to visually capture the problems.
All findings should be logged in reports, creating a comprehensive maintenance history that supports compliance and informed decision-making.
Note the Exact Location of the Issues
Precise documentation of the location and specifics of any issues encountered during heavy equipment inspection is critical for maintaining an accurate record of the machinery’s condition.
Identify Damage:
- Degree of damage
- Impact on operations
Faulty Equipment:
- Specific malfunctioning parts
- Potential for equipment failure
Maintenance Process:
- Steps for rectification
- Prioritization based on severity
Inspecting heavy equipment with precision ensures safety and optimizes repair efforts.
Capture Photos/Videos of Problems
To enhance the clarity and utility of heavy equipment inspection records, capturing high-quality photos and videos of any identified problems is imperative.
This visual evidence, integral to daily and performing inspections, supplements the equipment inspection checklist, ensuring no potential issues are overlooked.
Such detailed documentation helps prevent accidents, fostering a safer work environment while maintaining a meticulous record of compliance and maintenance history.
Log All Findings Clearly in Reports
Maintaining a comprehensive record of inspection findings is essential for tracking the condition and maintenance history of heavy equipment.
- Minimize human error
- Adjust the maintenance plan accordingly
- Prevent further damage
Using paper forms or digital systems, log inspections systematically, fostering a culture of care and attention to detail that goes beyond mere compliance, safeguarding efficiency and safety.
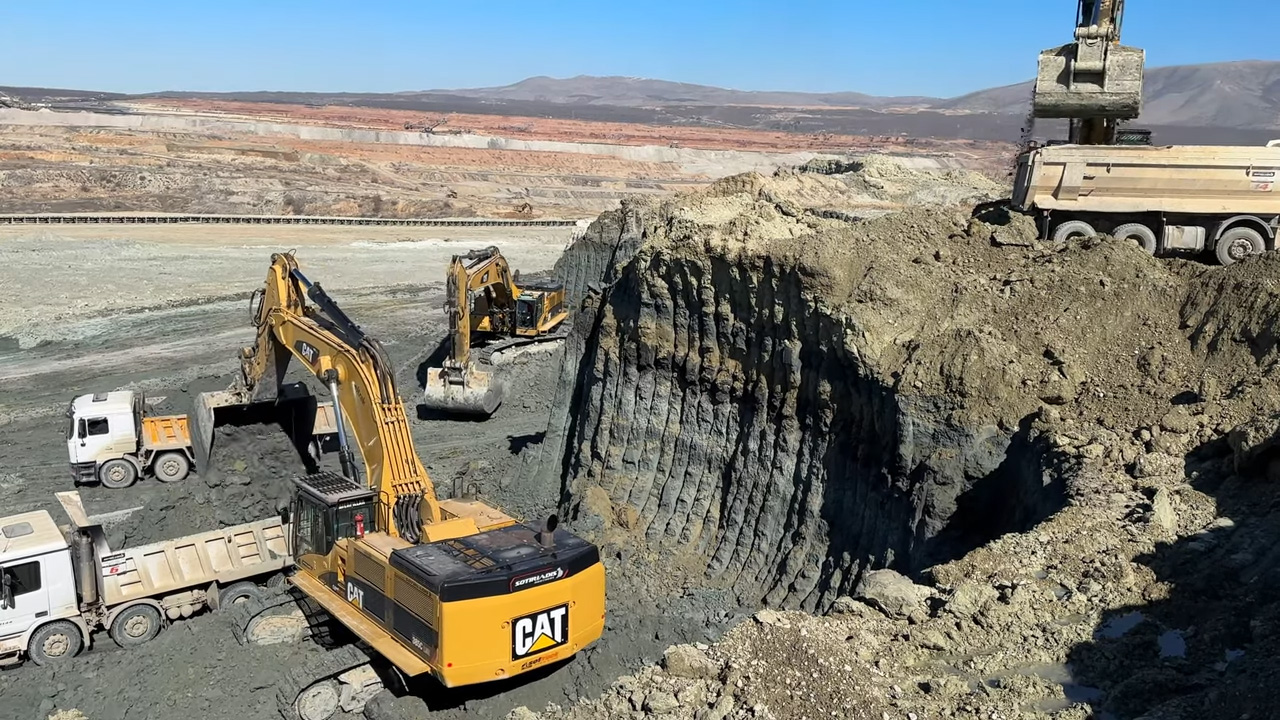
Address Issues Promptly and Completely
Once inspection reveals a problem, it is imperative to prioritize the most critical issues for immediate attention to maintain operational safety and efficiency.
Thoroughly implementing repairs and ensuring equipment is fully functional before its next deployment prevents the escalation of minor issues into major system failures.
A follow-up process to verify the effectiveness of the repairs and the resolution of the initial concerns is essential for long-term equipment reliability and compliance with regulatory standards.
Prioritize Critical Problems
When conducting heavy equipment inspections, it is crucial to promptly and thoroughly address issues that are identified as critical to ensure safety, maintain production quality, and minimize downtime.
Prioritizing Safety
- Protect operators from harm
- Avoid costly repairs through early detection
Recurring Issues
- Implement changes to prevent future occurrences
Optimal Performance
- Ensure equipment functions at peak efficiency
Implement Repairs Fully Before Next Use
Having established the importance of addressing critical problems during heavy equipment inspections, ensuring that all repairs are fully implemented and documented before the machinery is deployed for the next job is equally imperative.
Adhering to the manufacturer’s instructions, effective maintenance minimizes repair costs and assures the equipment’s optimal condition.
Timely rectification of issues, verified through inspection, is key to safety and efficiency.
Follow Up to Ensure Resolution
Addressing reported malfunctions and wear in heavy equipment without delay is crucial to prevent safety risks and ensure ongoing operational efficiency. Follow-up is key:
Periodic Inspections
- Identify issues early
- Address with particular attention
- Save money by preventing escalation
Equipment Safety
- Prevents accidents
- Preserves operator well-being
Resolution Efficiency
- Avoids downtime
- Maintains performance standards
Prompt resolution fortifies trust and underscores a commitment to safety and cost management.
Leverage Technology for Efficiency
Incorporating cutting-edge technology into heavy equipment inspections can significantly enhance operational efficiency and accuracy.
Inspectors can gain additional insights and capture detailed information that the naked eye might miss by utilizing sensors and cameras.
Moreover, maintaining digital logs and enabling mobile reporting ensures inspection data is readily accessible on-site and facilitates a more proactive approach to equipment maintenance.
Use Sensors and Cameras to Aid Inspections
Harnessing the power of sensors and cameras significantly enhances the effectiveness of heavy equipment inspections by offering real-time data and visual assistance.
Improve Productivity
- Streamline inspection processes
- Detect issues early for proactive maintenance
- Integrate data for comprehensive analysis
Best Practices
- Access hard-to-reach areas
- Capture detailed images
- Ensure accurate equipment assessments
Future Inspections
- Prepare for advanced digital solutions
- Establish a foundation for continuous improvement
- Anticipate equipment needs
Maintain Digital Logs for Easy Access
Transitioning to digital logs is a pivotal step in modernizing the management of heavy equipment inspection records for enhanced efficiency and accessibility.
Cloud-based solutions ensure that construction projects benefit from centralized maintenance logs. By automating systems, teams can regularly check equipment performance, a crucial part of upkeep.
Implementing technology solutions streamlines record-keeping and maintaining accurate, up-to-date documentation for safety and operational excellence.
Enable Mobile Reporting for On-Site Use
Embracing mobile reporting systems transforms the efficiency of on-site equipment inspections, allowing for instant, accurate data collection and communication. These tools play a vital role in:
Monitoring Equipment Performance
- Real-time updates
- Preventive maintenance alerts
Identifying Issues
- Loose bolts
- Wear and tear
Enhancing Job Site Safety
- Immediate reporting of hazards
- Swift corrective actions for heavy machinery
Mobile reporting ensures the integrity and safety of operations.