Heavy Equipment Tire Maintenance Tips
Meta Description: Regular maintenance is crucial to maximize tire life for heavy machinery. Learn tips to inspect tires for wear and proper inflation to avoid replacement costs and downtime.
Proper tire maintenance is crucial for heavy equipment operators. Fleet managers rely on their tires, from loaders to excavators, to work efficiently on job sites. However, heavy use in demanding conditions can quickly damage tires.
This guide provides rental companies and contractors with practical tips to maximize tire life, performance, and safety. Key areas covered include inspecting tires regularly, selecting appropriate tire types, promoting best driving habits, and leveraging new technologies to simplify maintenance.
Key Takeaways
- Understanding tire types and components and selecting the right models for equipment optimizes performance.
- Regular visual inspections, pressure checks, and tread measurements through established routines catch small issues before costly repairs.
- Choosing tires suited for applications and strategic maintenance like rotations prolongs tire life.
- Safe driving techniques and addressing issues promptly support tires enduring harsh conditions.
- Leveraging technology streamlines tasks while remote monitoring aids oversight of dispersed fleets.
- Developing structured inspection and replacement plans with trained staff to manage expenses predictably across sites.
Understanding Heavy Equipment Tire Basics
Understanding the basics of heavy equipment tires is essential for implementing an effective maintenance program. There are several key aspects rental companies and contractors should comprehend.
Common Heavy Equipment Tire Types
Heavy equipment tires come in two main varieties – bias and radial. Bias tires feature belts wrapped at alternating angles, providing a smooth ride but less traction.
They remain popular for their puncture resistance on sites with sharp debris. Radial tires have belts positioned straight across the tread for enhanced traction, handling, and fuel efficiency. However, their treads are more vulnerable to cuts.
Within these categories, tire manufacturers also produce type-specific models. For instance, loaders and bulldozers use tires with sturdier sidewalls and deeper treads for load carrying, traction, and smooth steering.
Scrapers and graders prioritize heat and wear resistance during heavy-duty tasks. Choosing the right tire type ensures equipment performs as intended while prolonging tire life.
Tire Components and Their Importance
Regardless of design, every tire contains basic components that maintain proper inflation and handling. The bead wires anchor the tire to the wheel rim, while steel belts reinforce the tread and disperse weight.
Polyester or nylon cord body plies further support these belts. An inner liner protects the casing from air leaks. Together, these parts allow tires to safely carry heavy loads during demanding jobs like digging and hauling.
Their condition directly affects safety, traction, and tire lifespan. Regular inspections help catch issues before structural damage occurs.
Properly understanding of tire construction, types, and each component’s role empowers fleet managers to select options for their equipment’s applications.
Combining the right tire models with regular maintenance routines like pressure checks and visual inspections helps maximize performance in varied terrains. This preserves tire investment while keeping fleets rolling productively between replacements or repairs.
Inspecting and Maintaining Tires Properly
Inspecting tires regularly is crucial for fleet operations. Close monitoring preserves tire investment and prevents accidents from undetected issues.
Performing Visual Inspections
Thorough visual inspections should be part of pre-trip routines. Operators must walk around their heavy equipment to examine each tire.
They check for irregular tread wear, cracks, cuts, bubbles, and other visible signs of damage on treads and sidewalls that compromise integrity. Any issues detected can then be addressed before becoming serious problems.
Checking Tire Pressure
Monitoring air pressure is equally important, as underinflation is a leading cause of premature wear and failure. Low pressure reduces load capacity and causes excessive heat buildup in rubber.
Fleet managers must ensure technicians and operators use a reliable pressure gauge to check psi levels weekly at a minimum and reinflate tires when needed, according to the manufacturer’s recommendation.
Evaluating Tread Depth
Treadwear also requires assessment. The tread provides traction, so operators need to measure depth regularly using a tread depth indicator.
Replacing tires becomes urgent once the tread falls below the wear indicator bars molded into the pattern. Running on bald tires risks losing control in demanding conditions like mud or snow.
Through consistent visual checks, pressure testing, and tread measurement, fleets can catch small issues before they escalate.
This prevents unnecessary downtime and accidents while extending the useful service life of valuable tires. Pairing regular inspections with the proper selection and maintenance routines helps maximize uptime.
Maximizing Tire Life Through Best Practices
Maximizing tire life starts with selecting the right models for each machine. Strategic maintenance practices and safe operation further preserve valuable tires.
Selecting the Right Tires for Your Equipment
Proper selection considers the equipment, its tasks, and work environments. For example, choosing bias or radial tires suited to digging vs. hauling ensures optimal performance.
Mixing tire types or using incorrect models for conditions can accelerate wear. Consult manuals to confirm load ratings, too.
Implementing Preventive Maintenance Procedures
Regular maintenance extends tire life. Beyond inspections, fleets should rotate tires periodically to promote even treadwear.
Timely wheel alignments control abnormal tire stresses from misaligned equipment. Promptly addressing issues like underinflation avoids costly damage. Retreading worn casings also saves costs while benefiting the environment.
Promoting Safe Driving Habits
How equipment is driven impacts tires as much as work conditions. Training operators in defensive techniques support tires.
Avoiding excessive speeds prevents dangerous heat buildup in rubber. Gentle braking and cornering reduces flat spots from abrupt stops and turns. Adhering to load limits preserves casing integrity as well. Selection, maintenance, and safe operation maximize tire lifespan through each phase of use.
Fleet managers who comprehensively manage these elements gain the most uptime per tire. Strategies like the above help contractors and rental companies control expenses while serving customers with well-maintained, productive fleets. Tires’ reliability remains critical for completing jobs efficiently in demanding environments.
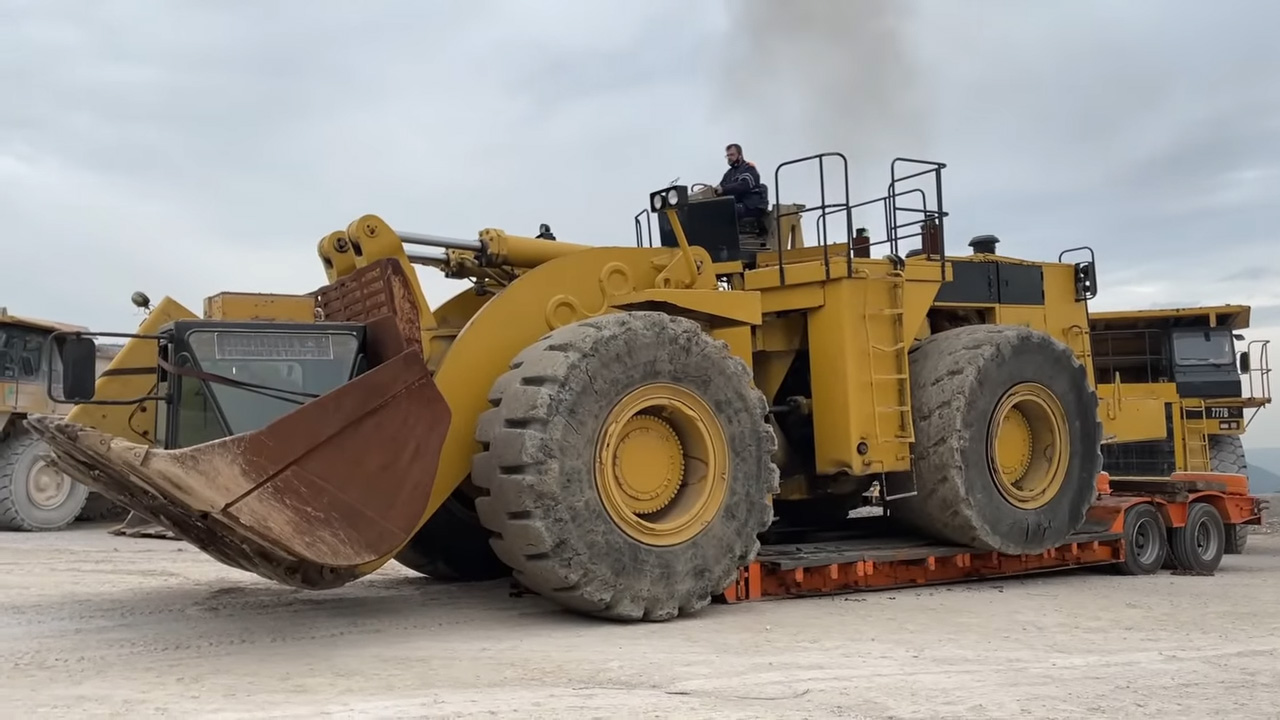
Using Technology to Simplify Maintenance
Leveraging technology streamlines maintenance programs. Telematics solutions provide real-time tire data for simplified monitoring.
Leveraging Telematics Solutions
Fleet managers rely on technology like tire pressure monitoring systems to remotely track pressures without manual inspections.
When paired with fleet management software, TPMS alerts managers to low pressures from a computer. This allows proactive responses rather than reactive repairs. Telematics also tracks machine runtimes and locations to schedule strategic tire rotations.
Benefits of Automatic Tire Inflation Systems
Automatic tire inflation systems automate air adjustments based on TPMS readings. Basic ATIS refills under-inflated tires as needed. Advanced systems also actively monitor for overinflation to prevent failures.
Such systems eliminate manual air checks while promoting even wear. Contractors save labor costs and downtime compared to traditional maintenance routines.
Technology streamlines previously time-consuming tasks. Telematics delivers constant tire monitoring to fleet managers’ desktops to oversee dispersed equipment easily.
Automatic solutions perform inflation tasks to keep fleets rolling productively. Combined with strategic maintenance plans, these innovations maximize uptime and lower operating expenses through simpler tire program administration. Contractors gain competitive advantages through optimized fleets.
Developing an Effective Fleet Management Program
Developing an effective fleet tire program requires strategic planning. A structured plan and trained team optimize maintenance outcomes.
Creating a Tire Inspection and Replacement Plan
A scheduled plan outlines inspection intervals based on tire type and work conditions. It establishes replacement criteria for tread depth and casing condition to avoid failures.
The plan pairs with a tire inventory and purchase schedule to ensure adequate stock for replacements or repairs.
Training Operators and Technicians Properly
All personnel involved in tire maintenance require guidance. Operators must understand inspection procedures and what issues to report.
Technicians need training on tire selection, mounting, demounting safety, and repair best practices. Training instills proper techniques while raising awareness of factors impacting tire life.
Fleet managers can further refine plans over time based on tire performance data. Regular reviews identify trends in wear rates by machine, site, or operator.
Digital solutions delivering real-time tire metrics aid management decisions. A proactive approach to inspections, replacements, record keeping, and staff education helps contractors maximize uptime at controlled costs.
Streamlined maintenance supports bids with predictable tire expenses factored inappropriately. A disciplined fleet program preserves profitability across changing job conditions.
Maintaining Tires for Optimal Performance
Tire wear, load-carrying capacity, and equipment safety depend heavily on strategic maintenance routines. Regular inspections and adjustments are essential, but additional practices can further maximize tire productivity and service lifespan. Fleet managers promoting consistent inspections alongside additional measures gain the most efficient returns.
Pneumatic tires experience natural wear from friction against road surfaces. However, excessive or uneven wear shortens usable life unnecessarily. Routinely rotating tires distribute this wear evenly across the entire tread pattern. Operators should swap positions at least every 6,000-8,000 miles to prevent premature failures from localized wear.
Loading techniques also impact wear rates. Overloading or unevenly distributing weight accelerates casing and tread degradation. Training employees on load-carrying capacity guidelines preserves structural integrity. Daily pre-trip checks help catch potential issues before critical damage occurs.
Promoting defensive driving habits protects tires as much as equipment. Excessive speed, rough terrain, and harsh braking generate dangerous heat in rubber through unnecessary stresses. Educating operators on techniques like slowing appropriately on rough patches or using engine braking uphill preserves structural durability.
Small contractors on tight budgets benefit greatly from maximizing available hours on each set of tires. Daily inspections and addressing issues promptly through repairs save replacement costs. Training staff raises awareness to spot early signs of problems like underinflation and prevent costly downtime.