How to Avoid Common Heavy Equipment Issues?
Meta Description: Prevent costly downtime! Learn essential tips to dodge frequent heavy equipment pitfalls in our expert guide. Keep your machinery running smoothly.
To avoid issues with heavy equipment at construction sites that lead to downtime, injuries, and costs, it’s crucial to implement preventive maintenance programs that include routine inspections, fluid checks, part replacements, and operator training. This protects construction workers by ensuring equipment functions properly despite extreme heat conditions, cold temperatures, and normal wear on internal components, metal components, and other parts that can cause erratic or mechanical failures if maintenance is neglected.
Key Takeaways
- Stick to a routine preventive maintenance program to catch small issues before they become mechanical failures.
- Regularly inspect for signs of wear and tear and promptly replace parts that show excessive wear to avoid breakdowns.
- Monitor fluid levels and regularly inspect for leaks to prevent serious mechanical issues.
- Learn how the different heavy equipment systems work together and recognize signs of wear or failure in these areas to prevent major component damage.
Common Heavy Equipment Issues
When dealing with heavy equipment, you’ll often face mechanical and electrical failures, structural damage, and fluid leaks.
Recognizing these common issues early is vital to prevent costly downtime and repairs.
Regular inspections and maintenance are your best defense against these persistent problems.
Mechanical failures
To keep your heavy equipment running smoothly, it’s essential to understand the most frequent mechanical failures and how to prevent them. Here’s what you need to focus on:
- Preventive Maintenance Schedule: Stick to a routine that checks critical components. Address small issues before they escalate into mechanical failures.
- Wear and Tear: Inspect for signs of deterioration regularly. Replace parts that show excessive wear to avoid breakdowns.
- Regular Maintenance: Keep engine oil and hydraulic fluids at optimal levels. Ensure clogged filters are cleaned or replaced to prevent overheating and other issues.
Electrical failures
While maintaining mechanical maintenance is crucial, don’t overlook the electrical components equally vital to your heavy equipment’s operation.
An electrical failure can leave you stranded, so watch for dashboard warning lights—your first hint that something’s amiss.
You’ll want to perform basic troubleshooting: check battery connections, inspect wires for damage, and ensure your alternator is charging correctly.
If you’re not adept with electrical systems, it’s wise to call in qualified technicians. They have the expertise to diagnose and fix complex issues.
Remember, preventive care is key—regularly check your electrical system to catch problems early.
This approach gives you control and can save costly downtime and repairs.
Structural damage
Bearing the brunt of heavy loads and rigorous tasks, your equipment’s structural integrity can suffer, leading to costly downtime if not addressed promptly. To prevent structural damage, it’s crucial to follow these steps:
Regularly inspect for signs of wear:
- Cracks in welds or the frame
- Rust and corrosion
- Bent or distorted components
Stick to appropriate operating procedures:
- Don’t exceed load limits
- Train operators on equipment handling
- Avoid harsh operating environments when possible
Undertake preventative maintenance:
- Schedule routine check-ups
- Lubricate moving parts regularly
- Promptly perform construction equipment repair when issues arise
Staying vigilant and adhering to these guidelines can save you from significant repairs and keep your machinery in top condition.
Fluid leaks
Just as maintaining structural integrity is vital for heavy equipment, it’s equally important to watch for fluid leaks, which can lead to serious mechanical issues if left unchecked. Your hydraulic system relies on hydraulic fluid to operate smoothly, and leaks can result in low hydraulic pressure, causing inefficiency or failure.
Regular fluid inspection is your best defense against this. It’s not just about spotting drips; you should also monitor fluid levels and check for insufficient lubrication, such as unusual noises or jerky movements. If you spot a leak, address it promptly to prevent further damage.
Understanding Heavy Equipment Systems
You’ll need a solid grasp of the main systems in heavy equipment to prevent downtime and costly repairs.
Start by learning how the engine, hydraulic system, drivetrain, and electrical system work together to power your machinery.
Recognizing the signs of wear or failure in these areas can save you from headaches.
Engine
To keep your heavy equipment running smoothly, it’s crucial to understand how the engine, the powerhouse of your machine, functions and what maintenance it requires. Here’s what you need to focus on:
Coolant Systems
- Check levels regularly to prevent overheating
- Inspect for leaks to avoid engine damage
Air Filter
- Clean or replace filters as needed to ensure clean airflow
- A dirty filter can lead to high fuel consumption
Engine Oil and Hydraulic Oil
- Monitor oil levels and quality to reduce wear
- Change oils according to the manufacturer’s schedule to maintain performance
Hydraulic System
After ensuring your engine is in top shape, it’s essential to focus on the hydraulic system, which powers various functions of your heavy equipment.
Regularly check the hydraulic pump for signs of wear or damage, as it’s the system’s heart. Adhering to a strict maintenance schedule can prevent most equipment malfunctions related to hydraulics. Remember, deterioration is often gradual; catching issues early can save you time and money.
Look for leaks, listen for unusual noises, and monitor system performance closely. By taking proactive steps, you’ll maintain control over your machinery’s hydraulic systems, ensuring they operate smoothly and extending the lifespan of your heavy equipment.
Drivetrain
Shifting the focus to the drivetrain, remember that the system transfers power from your engine to the wheels or tracks, making it a crucial component for your heavy equipment’s mobility. To prevent equipment failure, adopt these maintenance tasks:
- Regularly inspect drivetrain components
- Check for wear and tear on gears
- Ensure axles and shafts are aligned
- Look for any signs of mechanically induced failure
- Lubricate moving parts to reduce friction
- Use high-quality lubricants
- Follow the manufacturer’s recommendations for intervals
- Keep an eye on fluid levels
- Seek professional repair services for complex issues
- Don’t ignore unusual noises or vibrations
- Address leaks and seal problems immediately
- Rely on certified technicians for major repairs
Staying proactive will help you maintain control and avoid costly downtime.
Electrical System
Moving on to the electrical system, it’s essential to understand that this network powers your heavy equipment’s starting, operating, and safety functions.
To avoid construction equipment failure, be proactive. Regularly check for warning signs like dimming lights or erratic instrument readings, as these can indicate underlying issues. Poor maintenance is often the culprit behind equipment breakdowns. Therefore, you must implement a strict maintenance schedule.
Ensure that maintenance services include inspections of batteries, alternators, and wiring harnesses. Clean and secure connections prevent power losses and malfunctions.
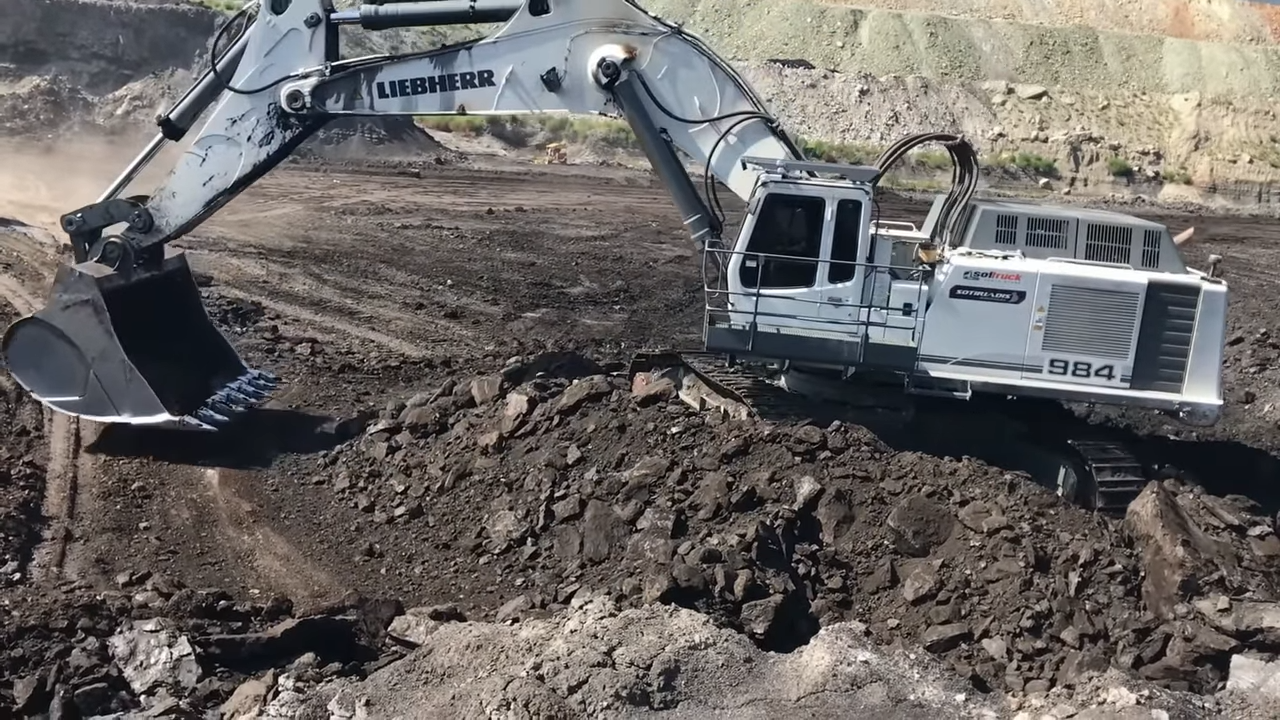
Root Causes of Equipment Reliability Problems
You can often trace most heavy equipment reliability issues to a few key culprits. If you’re not keeping up with preventive maintenance, you’re setting yourself up for breakdowns.
Additionally, improper operation and normal wear and tear over time will inevitably lead to problems, so understanding and addressing these factors is crucial for keeping your equipment in tip-top shape.
Lack of Preventive Maintenance
Neglecting regular preventive maintenance is often the primary culprit behind the unreliability of heavy equipment. To avoid equipment breakdown and minimize equipment downtime, you must stay on top of maintenance tasks.
Here’s how:
Implement Regular Check-ups
- Daily Inspections: Check fluid levels, tires, and brakes.
- Scheduled Services: Follow the manufacturer’s guidelines for service intervals.
- Component Checks: Pay attention to wear and tear on critical components.
Follow Standard Operating Procedures
- Use Checklists: Ensure all steps are followed without fail.
- Update Procedures: Adapt them as equipment and conditions change.
Ensure Proper Training
- Operator Training: Equip your team with knowledge of machine handling.
- Maintenance Training: Teach them to recognize early signs of potential problems.
Adhering to these preventive maintenance strategies will give you more control over your heavy machinery’s performance and longevity.
Improper Operation
Improper operation, a key root cause of equipment reliability issues, can lead to accelerated wear and tear and increased safety risks. To prevent such problems, you must thoroughly train your construction workers in the correct equipment operation.
Comprehensive operator training programs are indispensable. They don’t just cover the basics; they delve into the nuances that can make a big difference in longevity and safety.
Don’t let improper operation compromise your project’s success. Invest in training your operators; it’s a move that pays off by minimizing breakdowns and accidents.
Normal Wear and Tear
Over time, even the most robust heavy equipment will experience normal wear and tear. This natural process gradually deteriorates machine components and impacts their reliability. To maintain control and minimize the risk of machine failure, it’s crucial to understand the root causes:
Frequent Usage
- This leads to faster degradation
- Increases likelihood of common equipment malfunctions
Environmental Factors
- Extreme temperatures can accelerate wear
- Dust, moisture, and corrosive materials contribute to the deterioration
Age of Equipment
- Older machines may require more maintenance
- Replacement parts can be harder to find, risking prolonged downtime
Stay ahead of equipment failures by conducting regular inspections and following a strict maintenance schedule. This proactive approach helps you catch issues early, ensuring your heavy equipment remains reliable for longer.
Tips to Avoid Heavy Equipment Failure
You must establish a preventive maintenance program tailored to your machinery’s needs to stave off heavy equipment failure.
Ensure you’re operating the equipment correctly, as misuse can lead to premature wear and tear.
Stay vigilant, continuously monitor for deterioration signs, and promptly address issues to minimize downtime.
Implement a Preventive Maintenance Program
Establishing a robust preventive maintenance program is essential to reduce the risk of heavy equipment failure and extend the lifespan of your machinery. Here’s what you need to do:
- Schedule regular inspections
- Check for signs of wear and tear
- Identify potential mechanically induced failures
- Replace worn parts before they cause breakdowns
- Track service dates and repair details
- Monitor equipment performance over time
- Predict and prevent unexpected equipment failure
- Educate on the importance of daily checks
- Emphasize how proper handling prevents costly repairs
- Ensure everyone understands how to report issues promptly
Proper Equipment Operation
While implementing a robust maintenance program lays the foundation for equipment longevity, understanding and practicing proper equipment operation is equally crucial in preventing heavy equipment failure. You must handle your construction equipment carefully to ensure it functions properly. Always follow the manufacturer’s guidelines for operating any piece of heavy machinery. This means respecting load limits, speed recommendations, and operational procedures. Ignoring these can lead to undue stress on the equipment, resulting in mechanical problems.
Don’t cut corners or rush the process. Taking time to perform tasks correctly can save you from costly repairs or dangerous malfunctions. Remember, proper equipment operation isn’t just about following steps; it’s about cultivating a mindset of responsibility and attention to detail that keeps your machinery—and your project—running smoothly.
Monitor and Predict Wear and Tear
Monitoring your heavy equipment for signs of wear and tear is essential in predicting potential issues before they escalate into costly failures.
Regularly check for:
- Unusual vibrations or noises indicating erratic or intermittent failure
- Oil levels and quality to prevent major component damage
- Heat patterns that might signal thermally induced failure
You’ll pick up on small problems before they lead to equipment damage or unsafe conditions by staying vigilant. Use diagnostic tools and conduct visual inspections to detect anomalies.
Implement a maintenance schedule that includes the following:
- Frequent monitoring
- Predictive analysis
- Timely repairs
This proactive approach allows you to maintain control over your heavy equipment’s reliability and longevity, ensuring it remains a valuable asset to your operations.
Respond Quickly to Problems
Once you’ve identified a potential issue through regular checks, it’s crucial to act swiftly to prevent heavy equipment failure. Don’t hesitate; machines often fail due to ignored warning signs. Addressing problems promptly minimizes the risk of failure occurring at a critical moment, which can lead to significant downtime and costly emergency repairs.
You must respond quickly to problems to maintain control over your operations. Take immediate action if you notice any abnormal noises, leaks, or performance issues. Schedule repairs or maintenance as soon as possible. By being proactive, you fix the current issue and prevent potential future failures.