How Do You Troubleshoot Heavy Equipment – A Complete Guide
Meta Description: Learn how to prevent equipment failures through a comprehensive preventative maintenance plan, including inspection techniques, operator training, fluid analysis, and more.
Troubleshooting issues with heavy equipment is inevitable in keeping operations running smoothly. However, unplanned downtime can result in significant losses. This guide gives construction managers a simple process to diagnose problems at their roots. You’ll learn to recognize common failure types, implement a preventative maintenance plan, and properly care for machinery. Following these steps will help you identify issues quickly and prevent costly breakdowns.
Key Takeaways
- The three types of equipment failures are sudden, intermittent, and gradual. Recognizing these helps troubleshoot issues.
- Thermally-induced, mechanically-induced, and erratic failures are the top root causes. Understanding these allows for focused maintenance efforts.
- Implementing a preventative maintenance plan through a commitment to schedules, thorough inspections, operator training, and maintenance records prevents downtime.
- Methodically verifying problems, identifying root causes, fixing issues, and testing repairs streamline troubleshooting.
- Regularly monitoring fluid levels and quality, inspecting equipment internally and externally, and keeping service records aid in detecting problems early.
- Proper storage, watching for warning signs from operators, and avoiding misuse extend equipment lifespan.
- Complex electrical issues, intermittent problems, warranty repairs, or fleet assessments may require engaging qualified service providers for expertise.
Understanding the Types of Equipment Failures
There are generally three types of failures that can occur with heavy equipment: sudden failures, intermittent failures, and gradual failures. Construction managers need to recognize the signs of each to properly troubleshoot issues and prevent costly downtime.
Sudden Failures
Sudden failures happen without warning signs. Usually, the cause of sudden failure is obvious, such as a broken hydraulic hose or a failed electrical system. These failures require replacing or repairing the faulty component to return the equipment to service.
Intermittent Failures
Intermittent failures occur sporadically and can be difficult to diagnose. The equipment may stop working randomly under various operating conditions. Many intermittent failures are caused by electrical or hydraulic system overloads, especially with computerized components. These types of failures may need trial-and-error replacement of parts to isolate the root cause.
Gradual Failures
Gradual failures, if unaddressed, can develop into major issues. But they are entirely preventable with regular maintenance and inspections. As equipment ages, construction managers should note worn parts and components nearing the end of their lifespan. These parts should be proactively replaced before complete failure occurs. Following manufacturers’ recommended maintenance schedules and inspection intervals helps catch gradual failures early.
Some signs of an impending gradual failure include:
- Leaking hydraulic fluid from cylinders or pumps
- Worn engine belts that are glazed or cracked
- Fluid levels are low due to consumption or leaks.
- Increased vibration or noise from components
- Failure of seals or gaskets
- Electrical shorts or loose connections
- Excessive play in hoses, lines, or linkages
Catching gradual failures early allows managers to schedule downtime for repairs conveniently. This helps prevent unexpected breakdowns, reduces costly repairs, and extends the lifetime of equipment before replacement is needed. Recognizing the differences between sudden, intermittent, and gradual failures is important in properly troubleshooting issues and implementing an effective preventative maintenance program.
Learning the Root Causes of Failures
Three main types of root causes can lead to heavy equipment failures: thermally-induced failures, mechanically-induced failures, and erratic failures. Identifying the root cause is an important part of properly troubleshooting issues.
Thermally-Induced Failures
Thermally-induced failures occur when extreme fluctuations in temperature stress machinery. This includes large swings between hot and cold operating conditions. Temperature issues often happen when starting a cold machine in freezing weather or running equipment in very hot or cold environments outside its temperature design range. Symptoms may include cracked heads or blocks.
Some signs of impending thermally-induced failure include:
- Difficulty starting or loss of power at highs/lows
- Fluctuating engine temperatures
- Frost or condensation inside the engine compartment
- Steam from the radiator or exhaust
Mechanically-Induced Failures
Mechanically induced failures result from vibration, shocks, collisions, or overexerting equipment. These are generally easy to recognize and prevent through regular maintenance like lubrication, replacement of worn parts, and ensuring proper alignment of components. Mechanical failures may cause leaks, loose or sheared bolts, or damaged hoses/linkages.
Erratic Failures
Finally, erratic failures occur randomly and are difficult to predict. These types of failures usually stem from sudden electrical or hydraulic system overloads. Erratic issues may require troubleshooting techniques like trial-and-error parts replacement to isolate the root cause component.
Understanding the most common root causes of failures helps construction managers recognize warning signs. This allows them to schedule maintenance before small issues worsen. It also helps pinpoint where to focus preventative maintenance efforts to reduce downtime.
Implementing a Preventative Maintenance Plan
A preventative maintenance plan is crucial for reducing equipment failures and associated costly downtime. There are several aspects to consider when implementing an effective preventative maintenance program.
Committing to Regular Maintenance
Construction managers must be fully committed to performing maintenance at scheduled intervals. Regular maintenance catches small issues before they escalate and helps extend the lifespan of machines. According to manufacturers ‘ recommendations, managers should dedicate appropriate time and budget for tasks.
Inspecting Equipment Thoroughly
Proper inspections are important for identifying maintenance needs and catching problems early. Inspections should follow comprehensive checklists that cover the equipment inside and out, including fluid levels, hoses/belts, electrical systems, and safety components. Inspections provide opportunities to inspect worn parts for replacement before failure.
Training Operators Properly
Operator training is key so they understand their machine’s functions and limitations. Operators should know what types of inspections they are responsible for daily, like checking fluid levels and tightening components. They need to recognize warning signs and be trained in basic troubleshooting techniques.
Following Manufacturers’ Schedules
Equipment manufacturers provide maintenance schedules tailored to each machine model. These schedules outline the specific maintenance tasks and intervals recommended under normal operating conditions. Following OEM schedules ensures equipment functions as designed and is protected under warranty coverage.
Tips for implementing a preventative maintenance plan:
- Use maintenance checklists for consistency
- Involve operators in daily inspections
- Maintain service records in a database
- Order filters/fluids in advance based on schedules
- Outsource specialized tasks as needed
- Train new maintenance technicians
- Analyze breakdown trends to refine schedules
With a commitment to regular maintenance, thorough inspections, trained operators, and schedule adherence, a preventative plan keeps equipment performing productively for longer. This helps reduce repair costs and prevent unexpected downtime.
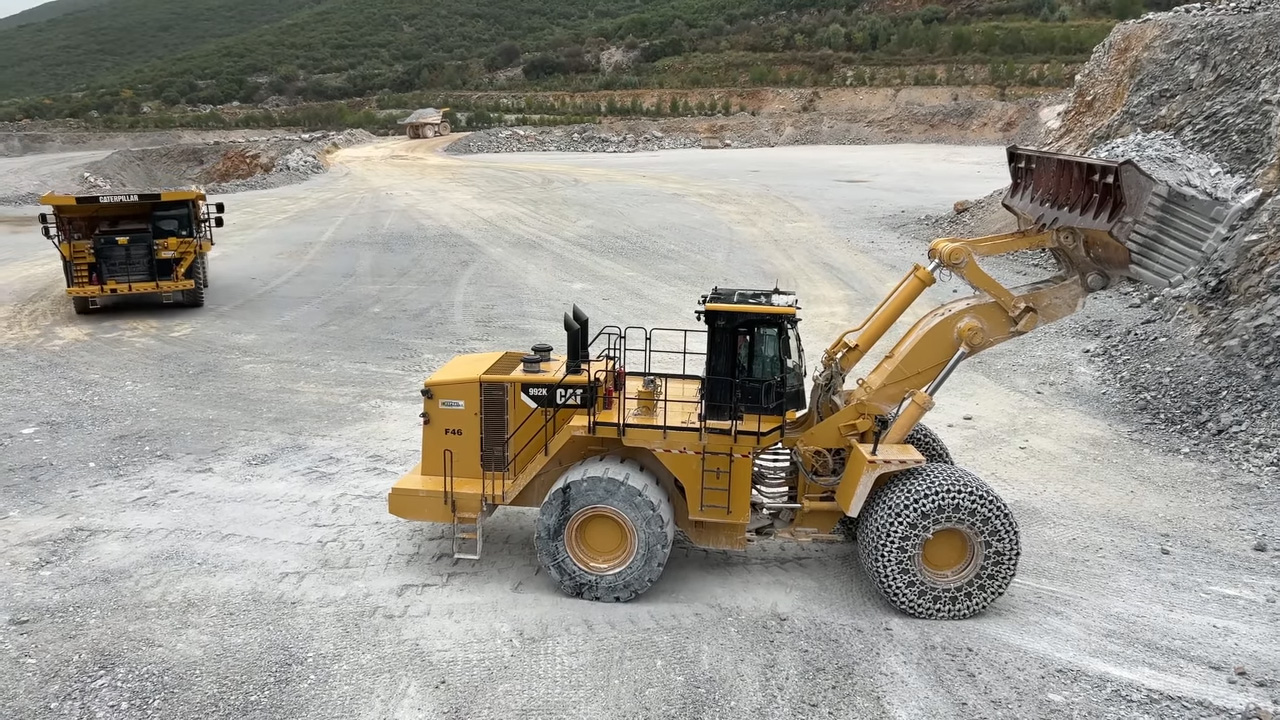
Developing a Site-Specific Preventative Maintenance Plan
Ensuring proper maintenance at each unique job site location is crucial for preventing equipment failures and downtime. Construction managers must develop preventive maintenance plans tailored to the specific operating conditions and challenges machinery faces at individual sites.
Many factors influence maintenance needs, such as the terrain equipment that must be traversed, weather extremes like extreme heat or cold temperatures, dust levels that can impact internal components, and the types of tasks machines perform, like heavy digging or lifting. Equipment used at quarries, for example, may experience more wear from dust exposure than machinery on road construction projects.
Managers can adjust maintenance schedules and on-site stock of filters, fluids, and parts by evaluating these environmental conditions, duty cycles, equipment functions, and operator experience levels. Inspection criteria should account for site-specific factors that could cause premature equipment breakdowns or failures. Schedules may need to be more frequent for job sites with harsher conditions.
Tailoring the plan also involves providing operator training suited to the anticipated challenges. For example, inexperienced operators working under difficult conditions may need additional instruction on pre-operation inspections, recognizing potential issues, and procedures to follow if machinery performance is affected.
Addressing Common Equipment Issues
Construction equipment experiences frequent problems that maintenance programs must be prepared to troubleshoot efficiently. Issues like unexpected shutdowns, intermittent hydraulic functions, electrical failures, and signs of mechanical trouble often indicate the need for repair or component replacement.
Thoroughly cleaning and inspecting battery terminals and electrical connections helps prevent costly downtime from corrosion or loose connections. Diagnostic testing aids in pinpointing faulty sensors, switches, or wiring that need replacement to restore functionality.
Low hydraulic pressure, leaks, erratic control response, and failed hydraulic pumps or valves usually stem from worn or blocked hydraulic filters needing replacement. Checking for air in hydraulic lines is also important to ensure the system can operate equipment properly under load.
Abnormal noises, fluid leaks, or increased vibration detected during inspections may signal impending mechanical failure of gearboxes, drive chains, or other moving parts. Inspecting these major components for cracks, alignment issues, or excessive wear helps catch problems before a breakdown occurs on the job site.
Detailed maintenance logs of repairs, component replacements, and inspection findings support identifying recurring issues on specific machinery. This helps construction companies refine preventive maintenance programs to minimize unnecessary repair costs and preventable downtime.
Knowing how to Troubleshoot Issues Effectively
Methodically troubleshooting equipment issues is crucial for quick and accurate diagnosis. Construction companies can minimize costly downtime by following a preventive maintenance plan with defined steps to properly identify and resolve problems. There are generally four key phases to the troubleshooting process:
Verifying the Problem
The first step is to confirm an equipment failure by speaking with operators about erratic performance issues, visually inspecting for abnormalities, and checking indicator lights and gauges. Comparing readings to manuals helps determine normal versus abnormal function. Proper training ensures technicians know what readings indicate a machine may not operate as intended.
Identifying the Root Cause
Once equipment failure is verified, the root cause must be isolated through running system tests, monitoring pressures and temperatures of hydraulic and engine systems, and inspecting mechanical and electrical components and fluid quality and levels. Tools like multimeters help evaluate electrical and intermittent failures within systems. Inspection aids in pinpointing the faulty component before further damage occurs from continued operation.
Correcting the Issue
Repairs or part replacement can begin following safety procedures with the identified mechanically or electrically induced failure. Replacing the suspected faulty engine oil filter, hydraulic pump, or electrical switch tests the diagnosis. An additional inspection ensures no related damage to other components occurs, requiring maintenance.
Testing the Repair
The repair is verified by retesting the full operation of the fixed system or area. Readings are compared to known good values from manuals or baseline measurements. Cycling all functions helps reveal any remaining issues before returning the improved equipment to the job site or rental fleet.
Troubleshooting Tips
Consult equipment manufacturers for diagnostic flowcharts, note error codes, and thoroughly document findings to establish maintenance logs and schedules tailored for each machine model. Partnering with local cat equipment dealers provides additional guidance for complex intermittent issues. Factory training aids technicians in restoring functionality quickly and minimizes costly downtime from unexpected failures in extreme weather conditions.
Closely Monitoring Equipment Conditions
Proactively monitoring equipment conditions is crucial for construction companies to identify issues early and prevent costly downtime. There are several key aspects to include in an effective monitoring program that utilizes proper preventive maintenance practices.
Checking Fluid Levels and Quality
Routine inspections ensure hydraulic systems and lubrication levels are properly maintained to prevent leaks that could lead to equipment breakdowns. However, regular fluid analysis identifies subtle wear through parameters like viscosity that fluid property tests detect before damage to components occurs. This helps construction managers schedule just-in-time maintenance to maximize uptime.
Inspecting External and Internal Areas
Thoroughly inspecting exterior checks for leaks or loose fittings to catch small issues before they worsen. Interior evaluations assess electronic components, hose, and wiring conditions for signs of wear. Involving operators in daily walkarounds through checklists catches minor issues. Their tips aid in troubleshooting intermittent failures.
Documenting Service Records
Recording all inspections, repairs, fluid changes, and parts replacements create a complete service history to refine preventive maintenance schedules. Documenting findings detect patterns to minimize unexpected equipment failures from improper maintenance in extreme weather conditions. Maintenance logs support warranty claims and resale value.
Additional Tips
Photographing unusual findings aids repairs. Fluid analysis trends identify machinery issues over the equipment’s lifetime. Proper training ensures technicians recognize abnormal wear before a major component failure occurs on the job site. With regular condition monitoring, construction firms efficiently resolve issues when convenient to maximize uptime through an effective preventive maintenance program.
Ensuring Proper Equipment Care
Beyond maintenance and inspections, properly storing and operating equipment is important for maximum life expectancy.
Storing Equipment Correctly
Equipment should be cleaned, stored indoors if possible, and protected from environmental factors when not in use. Sheltering prevents corrosion from water/salt exposure. Covers protect from pest damage and foreign object intrusion.
Watching for Warning Signs
Operators should monitor gauges and controls for any abnormal readings. Early signs like fluctuating temperatures or unusual noises/vibrations indicate potential issues. Noting these warnings allows proactive maintenance before failure occurs.
Avoiding Misuse and Abuse
Operating machinery within its intended design capacity prevents mechanical and thermal damage. Overexerting or misapplying equipment stresses components unnecessarily. Ensuring operators follow safety protocols with certified training helps reduce accidental damage from improper operation.
Additional Tips:
- Lubricate and fill all systems before seasonal storage
- Inspect stored units periodically for interior condensation
- Promptly address operator-reported signs of deterioration
- Use equipment manuals for guidelines on applications/limits
- Consider environmental factors for each job site
With diligent attention to storage, operation practices, and operator support, construction managers can maximize the lifetime heavy assets provide. Consistent, proper preventative care helps prevent downtime from misuse and conditions deterioration.
When to Seek Expert Assistance
While regular maintenance and inspections prevent many issues, some equipment problems require specialized expertise. Knowing when to engage equipment professionals can help address complex problems efficiently.
- Seek assistance for intermittent or recurring issues that can’t be resolved through standard troubleshooting. Experts have extensive diagnostic tools to isolate elusive problems.
- Consult experts for electrical/electronic systems and hydraulic or engine overhauls that involve disassembling major components. Proper reassembly is critical for these complex systems.
- Involve dealer technicians for repairs still under warranty. Their familiarity with your machine model helps ensure warranty coverage isn’t jeopardized by improper fixes.
- Outsource maintenance for job site equipment right before seasonal start-ups. Experts thoroughly inspect all systems to catch any winterizing issues.
- Consider expert fluid analysis for fleet-wide condition assessments. They detect subtle changes invisible to basic inspections.
- Engage training from manufacturers for new equipment, operators, or maintenance staff. Proper instruction on intended operation prevents premature wear.
Knowing your maintenance limitations and partnering with qualified service providers results in repairs that meet standards. This helps avoid costly mistakes or equipment downtime from issues beyond your technical scope.