Importance of Heavy Equipment Inspections
Meta Description: Regular heavy equipment inspections are crucial for construction businesses. They enhance safety, prevent downtime, and save costs. Discover the benefits of proper maintenance.
Regular inspection and maintenance of heavy equipment are crucial for construction buMeta businesses for several important reasons. Whether it is equipment used in roadwork, excavation, or lifting heavy loads, proper checks can help detect potential issues early on.
This can lower repair costs, reduce downtime, and prevent accidents. Safety should always be the topmost priority, especially in dangerous industries like construction that rely heavily on machinery.
Key Takeaways:
- Regular inspections are crucial for detecting issues early and preventing costly breakdowns.
- They help maximize safety for operators and other workers on construction sites.
- Inspections reduce unplanned downtime and ensure projects are completed on schedule.
- Partnering with local equipment dealers provides expert technicians and customized inspection checklists for optimal maintenance.
Importance Of Heavy Equipment Inspection
Regular inspections of heavy equipment are crucial for ensuring safety, compliance, preventive maintenance, and optimal performance. Comprehensive inspections deliver significant benefits in multiple areas.
- Safety: Inspections identify potential hazards and mechanical issues before they can cause accidents. Worn or faulty components are repaired or replaced to minimize safety risks. Issues are addressed proactively to reduce the likelihood of workplace incidents and injuries.
- Compliance: Inspections verify adherence to industry regulations and standards. Meeting regulatory requirements avoids penalties and ensures safe operations. Businesses gain legal protection and peace of mind operating within compliance.
- Preventive Maintenance: Inspections allow early detection of problems like leaks or malfunctions. Concerns can be promptly addressed through preventive repairs and replacements. This saves money by preventing costly breakdowns and future repairs.
- Longevity and Reliability: Addressing issues promptly extend the functional life of equipment. Proactive maintenance through inspections ensures sustained operational reliability.
- Performance and Productivity: Well-maintained equipment operates more efficiently. Performance is optimized to increase productivity and reduce downtime. Fewer delays enhance overall operational effectiveness.
Comprehensive heavy equipment inspections are a strategic investment that facilitates safety compliance, preventive maintenance practices, and optimal performance. This multifaceted approach delivers significant long-term financial and operational advantages.
Detecting Potential Issues Early to Prevent Equipment Failure
The construction industry relies heavily on machinery operating in demanding conditions. While equipment is built to last, continuous use and exposure to job site elements can cause gradual wear and tear of components over time.
Regular inspections allow any problems to be caught before they escalate into major and costly breakdowns. By scheduling inspections at recommended intervals, potential issues can be identified and addressed proactively.
Identifying Electrical and Mechanical Faults Before They Cause Breakdowns
Technicians perform thorough checks of critical systems during inspections. They closely examine the engine, hydraulic, and fuel systems for signs of fluid leaks, loose connections, or excessive wear.
Electrical wiring, sensors, and computer modules are inspected for damage, corrosion, or loose terminals that could impact performance over the long run. Identifying small issues like loose belts, hoses, or frayed wires allows them to be repaired before resulting in a system failure.
Catching defects early helps avoid equipment downtime for unexpected repairs during busy work periods.
Lowering Repair Costs by Catching Small Problems Early
Inspections also focus on structural components like frames, booms, buckets, and undercarriages that endure continuous stress. Cracks, deformation, or corrosion in load-bearing areas are repaired before escalating further due to continued operation. Similarly, brake pads, filters, and wear items are checked against manufacturer specifications.
Replacing them at the first signs of nearing end-of-life helps reduce lengthy repairs for complete component replacements later. Addressing small problems as they arise saves money versus neglecting maintenance until a major overhaul is needed.
Detecting Potential Issues Early to Prevent Equipment Failure
The construction industry relies heavily on machinery operating in demanding job site conditions. While equipment is built for tough work, continuous use can cause gradual wear over time. Regular inspections allow any developing issues to be identified before costly breakdowns occur.
Identifying Electrical and Mechanical Faults Before They Cause Breakdowns
During thorough checks, technicians closely examine critical systems for signs of trouble. They inspect the engine, hydraulics, and fuel systems for fluid leaks or excess wear that could impact performance.
Electrical wiring, sensors, and modules are also analyzed for damage or loose connections that may lead to future faults. Catching small problems like loose hoses or belts early allows timely repairs, avoiding unexpected repairs mid-project.
Technicians pay close attention to components under high stress. Structural areas like frames and booms that endure heavy lifting are inspected for cracks, deformation, or corrosion.
Early detection of such defects prevents further escalation with continued use over time. Similarly, brake pads, filters, and wear items are checked against specifications. Replacing them proactively reduces the risks of component failures down the line.
Lowering Repair Costs by Catching Small Problems Early
Addressing small issues as they emerge saves money versus neglecting maintenance. Inspections focus on preventing equipment downtime for unexpected component replacements or overhauls. Identifying electrical or fuel leaks early avoids costly engine damage.
Loose terminals or sensors catching problems in computer modules help prevent unnecessary repairs. Regular inspections can also minimize equipment repairs and maximize its resale value later.
By scheduling inspections at recommended intervals, potential faults can be addressed promptly before major failures occur. This improves equipment reliability while lowering long-term repair expenditures.
Reducing Unplanned Downtime and Associated Costs
Construction projects are subject to tight deadlines and budgets. Unforeseen equipment issues can disrupt work schedules and increase costs. Regular inspections aim to minimize such downtime through planned maintenance.
Keeping Equipment Running Smoothly to Meet Project Deadlines
Inspections play a key role in preventing unexpected breakdowns that halt progress. By proactively addressing small faults, performance and reliability are ensured long-term.
Technicians closely examine high-wear components like engines, transmissions, hydraulics, and electrical systems to avoid sudden failures. This allows smooth operation without unplanned repairs disrupting construction schedules.
Minimizing Downtime Through Planned Maintenance
Inspections also catch defects before they require lengthy repairs. Minor issues identified during routine checks are repaired quickly versus major repairs for neglected problems. Scheduled services like fluid changes, filter replacements, and part inspections are done regularly during planned downtime.
This minimizes unplanned downtime spent making unanticipated repairs in urgent situations. Overall equipment uptime and productivity are increased through preventative maintenance detected via thorough inspections.
By detecting red flags early, costly disruptions due to equipment downtime are avoided. This keeps projects on schedule through reliable machinery performance.
H2: Compliance with Industry Safety Standards and Regulations
Construction worksites have strict protocols to ensure worker protection. Regular equipment inspections help meet occupational safety and health guidelines. Technicians inspect for compliance with regulations during thorough examinations.
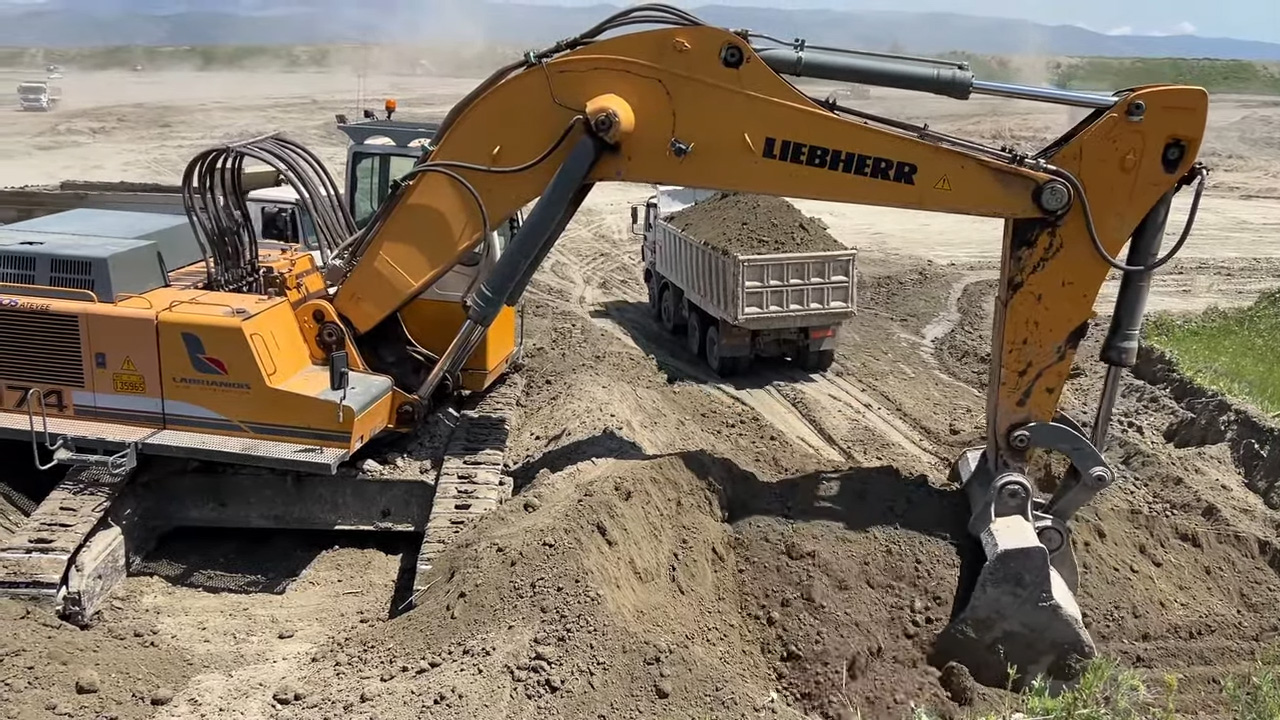
Extending the Lifespan of Equipment Through Proper Maintenance
Heavy investment in machinery can be protected through preventative care and inspections. Catching small issues early extends machine life significantly.
Replacing Worn Parts Regularly to Avoid Costly Replacements
Inspections catch components nearing end-of-service thresholds. Replacing brake pads, hoses, and bearings according to wear limits avoids more extensive repairs. This improves equipment reliability long-term.
Following Manufacturer Maintenance Schedules
Inspectors check machine hours and refer to OEM service manuals for recommended maintenance intervals. Conducting repairs and component swaps per schedule maximizes equipment life and resale value. Planned downtime minimizes production losses compared to unpredictable breakdowns.
Regular inspections play a key role in compliance, safety, and protecting the investment in heavy machinery through preventative maintenance best practices.
Benefits of Working with Local Equipment Dealers for Inspections
Proper inspections are key in maximizing equipment uptime, reliability, and safety. While in-house technicians can perform basic checks, an authorized local dealer offers various advantages.
Their factory-trained experts have extensive experience with your machine models. Dealers are also equipped with the latest diagnostic tools and access to manufacturer information.
This enables comprehensive inspections that cover all critical components and systems. Using OEM-authorized parts also helps meet compliance and warranty requirements.
Access to Certified Technicians and Genuine Spare Parts
Dealer technicians complete regular training and certification courses to keep up with the latest design changes. They can thoroughly inspect machines for electrical, mechanical, or structural defects. Their in-depth knowledge of your equipment model helps catch small issues before they escalate and cause costly damage.
Dealers also have direct contact with manufacturers for technical support. They stock an extensive inventory of genuine OEM parts for repairs and replacements. Using authentic components is vital for safety-critical systems. It also avoids invalidation of warranties and certification.
Dealers Can Provide Customized Inspection Checklists
Dealers also develop customized checklists specific to your machinery and industry based on OEM service manuals. A standardized process ensures a high-quality and consistent inspection each time. Inspectors methodically examine all major systems and components based on operating hours, applications, and environment.
The comprehensive checklist acts as a guide to avoid overlooking any small defects. Customization also allows flexibility to focus on areas requiring more frequent checks. Detailed inspection reports keep comprehensive maintenance records for compliance and resale value.
Partnering with an experienced local dealer ensures thorough equipment inspections. Their expertise, certification, and access to genuine parts deliver maximum uptime safely at lower overall costs.