Tips For Renting Heavy Equipment The First Time
Meta Description: Renting heavy equipment for the first time? Learn essential tips for a smooth, cost-effective rental, from equipment selection to safety protocols and cost-saving strategies.
Renting heavy equipment for the first time can feel overwhelming without proper guidance. This guide provides essential tips for a smooth, cost-effective first-time heavy equipment rental.
It outlines a step-by-step process for selecting the right equipment, understanding rental agreements and insurance needs, safely operating machinery, maintenance requirements, return procedures, potential additional expenses, and ways to save on costs. Let’s get started!
Key Takeaways:
- Carefully select the right equipment for each job and inspect machines thoroughly before use.
- Understand insurance maintenance requirements and thoroughly review rental agreements.
- Ensure all operators are properly trained and certified to use equipment safely.
- Carefully plan projects, maximize productivity, and ask about discounts for frequent rentals.
- Properly maintain and care for equipment, returning it cleaned in agreed condition.
Equipment Selection
The first critical step for any first-time heavy equipment rental is selecting the right equipment. Proper equipment selection is vital to efficiently complete tasks while avoiding costly downtime from mechanical issues or an inability to perform specific jobs.
This section will outline the critical factors to consider regarding your specific project needs, determining the required equipment specifications, and thoroughly inspecting machines before agreeing to a rental contract.
Consider Your Project Needs
Carefully assessing the scope of tasks, job site conditions, project timeline, and tight work areas is crucial to determining the appropriate equipment.
For example, excavating a large area may require an excavator, while smaller jobs like landscaping may be suited for equipment like skid steers. Considering your specific needs upfront will help narrow options to machines that can best handle tasks productively and cost-effectively.
Determine Equipment Specifications
With project needs in mind, carefully evaluate required equipment specifications. Key factors include engine horsepower, operating capacity, attachment compatibility, safety features, etc.
The right size is important—too small can increase costs from lower productivity or needing multiple machines, while too large may be overkill or unable to fit in tight spaces. Consultation with rental providers ensures the selection of premium machines from leading manufacturers that meet or exceed specifications.
Inspect Equipment Thoroughly
Upon delivery and before signing rental contracts, thoroughly inspect all equipment for any existing damage, wear, or issues. Check hydraulic and fuel systems, moving parts, and safety mechanisms, and ensure all requested attachments are included and in good condition.
Note any existing issues that could impact costs with repair fees upon return. Photographing problem areas ensures proper documentation to avoid assumptions of responsibility later. This upfront diligence avoids potential costly mistakes.
Rental Equipment Agreement Process
Finalizing the rental agreement process is important to understand obligations and avoid costly mistakes. This involves carefully reviewing insurance standards and contractual terms and conditions with rental providers.
Proper coverage protects against liability, while contractual reviews ensure clarity on responsibilities for maintenance, repair costs if damage occurs, and other potential fees. Let’s explore these vital aspects in more detail.
Understand Insurance Requirements
Nearly all rental companies require renters to hold active commercial general liability insurance, often with a minimum coverage of one million dollars, to protect against any injuries or property damage that might occur during equipment operation.
Investigate options for obtaining a short-term rental insurance policy through the rental company or your provider.
Be sure all operators are properly certified and licensed to reduce risks and premiums. Maintaining the necessary coverage ensures protection against financial losses from accidents and compliance with contractual obligations.
Review Contract Terms and Conditions
Thoroughly read all rental contracts, paying close attention to clauses around responsibilities for repairs, maintenance schedules, fueling requirements, overtime fees, damage coverage, and more. Understand if you are liable for repair costs from normal wear and tear versus accidental damage.
Clarify procedures for extensions or equipment returns outside standard hours. Ask questions about unclear terms to avoid assumptions leading to unexpected charges later. Negotiating rates upfront for volume rentals over a long-term project or for repeat customers of a rental company can also offer savings.
Operating Equipment Safely
Safety should always be the top priority when operating any heavy machinery. Accidents can cause significant injuries, liability issues, and costly repairs or downtime.
This section focuses on the importance of proper training and certification and diligently following best safety practices to avoid risks while maximizing productivity. Let’s explore these crucial aspects for maintaining a safe worksite.
Ensure Proper Training and Certification
Nearly all rental providers require evidence of certification showing equipment operators have completed proper safety training courses. These may include OSHA certifications for excavation, scaffolding, or lift operations.
Training ensures an understanding of machine capabilities and limitations, while certification demonstrates operators can safely control specific equipment. It may even qualify for reduced insurance rates.
Renters should only allow properly certified personnel to operate machinery and closely supervise any trainees to minimize risks and avoid accidents that could damage expensive equipment or injure workers.
Follow All Safety Protocols
Once on a job site, diligently practicing safety should be a top priority. This involves properly using personal protective equipment like hard hats, steel-toed boots, and high-visibility vests.
All safety mechanisms and operational protocols outlined in equipment manuals must be followed, including pre-operation inspections, avoiding overloaded or unstable working conditions, and never operating under the influence.
Keeping a safe distance from power lines when using elevated machinery is also critical. Taking the necessary precautions helps avoid costly repairs and fines and protects workers.
Maintenance and Daily Use
Proper maintenance is vital for equipment reliability, maximizing rental value, and avoiding costly repairs. Renters must conduct thorough pre-operation checks daily and follow any preventative maintenance schedules required by rental agreements. This ensures early detection of issues before they worsen and disrupt project timelines. Let’s examine these crucial maintenance tasks in detail.
Perform Pre-operation Checks
Comprehensive pre-operation checks should be conducted during every workday or shift change. This involves inspecting fluid levels, tire pressure, hydraulic and electrical systems, and safety mechanisms and checking for leaks, loose components, or unusual noises/vibrations.
Immediately address minor issues to avoid expensive repairs down the line. Maintaining detailed inspection records also demonstrates due diligence if repairs are needed later. Following checklists from equipment manuals ensures a consistent process for early problem identification.
Follow Preventive Maintenance Schedule
Rental agreements may require adherence to a preventative maintenance schedule set by manufacturers, such as completing scheduled fluid changes, filter replacements, and greasing components after a set number of operating hours. Sticking to this schedule preserves the long-term value of expensive equipment and prevents avoidable breakdowns.
Renters should keep detailed maintenance logs and receipts if rental providers request documentation. Outsourcing scheduled maintenance to certified technicians ensures quality parts and workmanship, avoiding issues caused by unqualified labor down the line.
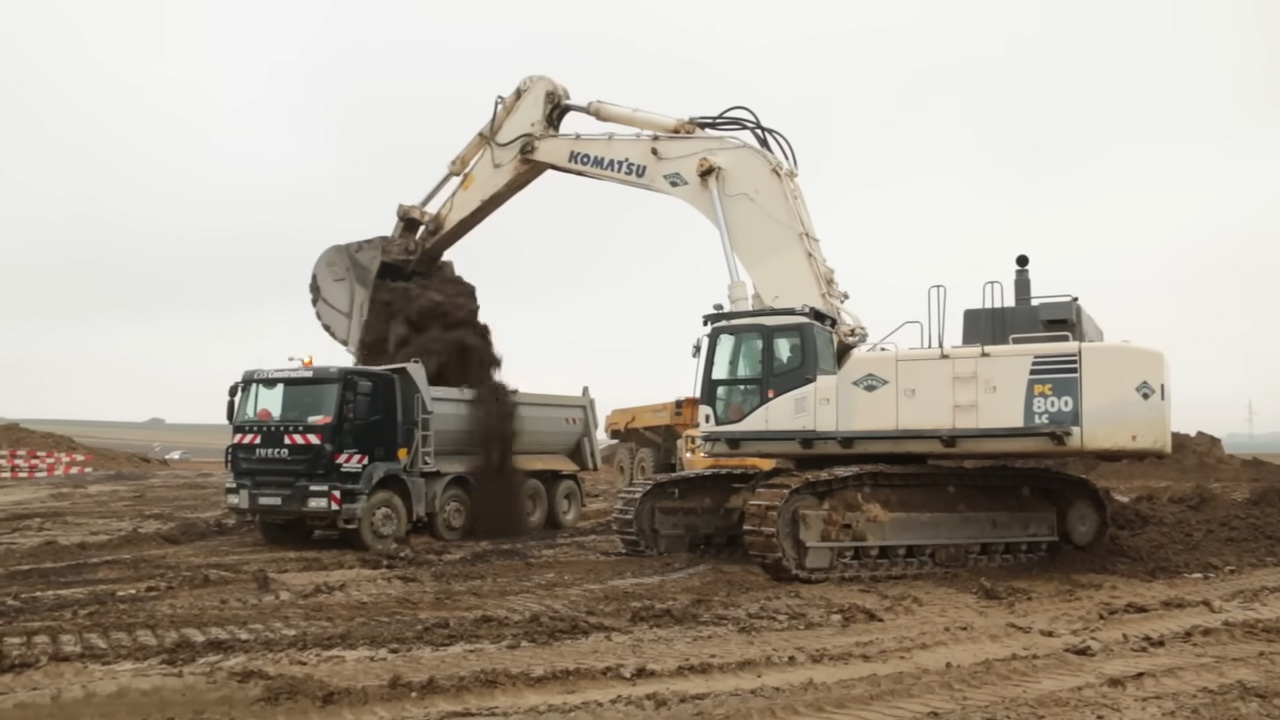
Return Procedures
Handling returns professionally ensures the highest chances of positive rental references and potential volume discounts on future projects. This involves thoroughly cleaning equipment and documenting any existing damage or repair needs. Let’s examine these crucial end-of-rental tasks in detail.
Clean Equipment Properly
Rental agreements require machinery to be returned in a similar condition as received. This means removing debris, mud, or materials from undercarriages, tracks, buckets, and interior cabins.
Pressure washing or using solvents for harsh residues helps speed up the inspection process and quickly gets equipment back into the rental fleet for the next customer. Some companies may charge cleaning fees for machines returned in unsatisfactory condition.
Note Any Damage or Issues
Carefully inspecting equipment for pre-existing versus new damage protects from unwarranted fees. Photograph and list any issues, dents, or repairs needed with estimated repair costs to submit. Negotiate responsibility for normal wear versus accidental damage.
Returning machinery with empty fuel tanks or a full service also demonstrates respect for the next renter’s time. Overall communication and honesty build credibility and influence potential references for future projects.
Additional Expenses to Expect
While rental rates provide equipment access, hidden costs can impact budgets if not anticipated. This section examines common additional fees associated with rentals like fuel, transportation, and potential repair charges. Factor these expenses into project estimates to avoid cost overruns. Let’s explore these items to allocate funding properly.
Fuel and Transportation Costs
Rental contracts typically require customers to refuel machinery before returning it. Budget accordingly based on fuel type, machine size, and planned operation hours. Transporting equipment also requires planning—more oversized items may necessitate flatbed trucks and permits.
Rental providers can assist with hauling logistics, but these services come at an additional cost. For longer-term rentals, on-site fuel storage and a project vehicle can minimize transportation expenses over the life of a job.
Potential Damage Fees
Accidental damage occurs, so understand liability policies. While some contracts waive fees for the first incident, subsequent repairs are usually the renter’s responsibility. Budget a contingency to cover repair costs from operator error to avoid exceeding estimates. Photograph and document pre-existing damage to avoid charges.
Consider optional damage waivers, though these increase rates. Proper training, maintenance adherence, and following safety protocols help prevent equipment damage and unnecessary charges that cut into project margins.
Tips for Cost Savings
Maximizing value from equipment rentals requires exploring strategies to reduce total costs. This final section suggests leveraging rental time frames and inquiring about volume discounts with providers. Implementing these techniques helps stretch budgets further on construction and land development projects.
Consider Rental Time Frame
Rates often decrease the longer a rental period. Monthly versus daily rentals offer substantial savings. Investigate purchasing or renting-to-own options for larger, long-term projects, which may prove more cost-effective in the long run.
Confirm equipment availability before making multi-month commitments. Short-term daily needs may be better served through alternative rental options. Understanding time requirements enables choosing the most economical framework.
Ask About Volume Discounts
Rental companies commonly provide discounts for frequent, high-volume customers. Inquire about tiered pricing for multiple concurrent rentals or anticipated long-term project needs. Volume commitments sometimes qualify for 5-15% off standard rates.
Build relationships with local rental providers—discussing anticipated equipment needs over the next six to twelve months allows for negotiating customized package deals incorporating discounts. Honest communication fosters partnerships that save money while supporting equipment access throughout project lifecycles.
Choosing the Right Rental Provider
Selecting the proper equipment rental provider is instrumental to having a smooth experience. While the lowest rates may seem attractive, hidden costs or lack of support can negatively impact projects. Consider choosing a company with a proven track record that invests in quality, certified staff, and well-maintained fleets.
Larger, national rental firms with extensive branch networks offer maximum equipment selection across all power classes to suit various job requirements.
This ensures the right machines are available when needed to avoid project delays. Their extensive rental fleets provide backup options if primary units require service. Large providers also offer consolidated billing and volume discounts for frequent customers.
However, smaller, locally-owned yards have advantages, too – often with more personalized customer service and flexible contract terms. Their proximity minimizes equipment delivery/pick-up times and costs.
Building strong relationships with these regional providers fosters honest communication and a thorough understanding of individual needs over multiple projects. Renters are treated more like partners than just a number.
Evaluate rental yards considering factors like maintenance/repair response times, certification qualifications, and availability of training/support services. Optimal providers invest in well-trained, experienced staff that can offer expert equipment guidance.
Their commitment to safety, certifications, and operating standards helps protect workers and equipment. Comprehensive insurance policies also offer peace of mind.