Compactor vs Road Roller – Key Differences for Your Project
Meta Description: Understand the critical differences between rollers and compactors to choose the right heavy equipment for your following construction equipment or project. Which compacting machine is best – roller or compactor?
When preparing for construction projects, choosing the correct compaction equipment is essential. This affects project quality and budget. While rollers and compactors are both used for soil densification, they differ in operation and suitability.
This article analyzes the key differences between these machines to help construction managers and contractors select the appropriate option for their needs. The focus is on equipment function, applications, and performance to aid decision-making.
Key Takeaways
- Rollers are large ride-on machines used for large-scale compaction like road construction, while compactors are smaller walk-behind machines for compacting in confined spaces.
- Rollers work by the weight of their drum and provide smooth, even compaction over a wide area. Compactors use a vibrating plate or ram for high-impact compaction in trenches or around structures.
- Choosing the right machine depends on the size of the project and site conditions. Rollers are best for open areas, while compactors are highly maneuverable for compacting in tight spaces.
Roller vs. Compactor – Key Differences Explained
Whether preparing the ground for a construction project or maintaining existing infrastructure, choosing the right compaction equipment is essential. Rollers and compactors are commonly used machines, but understanding how they differ can help contractors select the optimal option for the job.
How Each Machine Achieves Compaction
Rollers rely on static weight distribution or induced vibrations to compact materials. Their large, ride-on drums achieve compaction through repeated rolling passes that exert steady pressure. This compresses air pockets and locks particles into place. Vibratory rollers add an oscillating function for more effective compaction of cohesive soils.
Compactors use repetitive impact forces rather than steady pressure. Plate compactors transfer power from their vibrating steel plates through short, sharp movements. This allows them to displace air between material particles. Rammer compactors function similarly through their reciprocating rams. Both types deliver high-intensity compaction energy in short bursts, ideal for compacting trenches and other confined areas.
Common Types of Rollers and Compactors
There are several roller variations depending on the drum design. Smooth drum rollers are suited to granular soils and materials, while Padfoot rollers can handle cohesive soils. Tandem and pneumatic-tired rollers provide specialized functions.
Compactors also come in different styles. Pedestrian-operated plate compactors are versatile for paths and other small jobs. Larger vibrating and rammer models offer higher outputs. Landfill compactors feature corrosion-resistant components for waste applications.
Using static weight or induced vibrations, rollers provide efficient flatwork compaction over large surface areas. Compactors are better for irregular surfaces and tight spaces, delivering high-impact compaction through short, sharp movements of their plates or rams. Understanding these fundamental differences in how each machine achieves its compaction results enables contractors to select the right soil compaction equipment for any project scope and conditions.
Applications of Rollers and Compactors in Construction
Rollers and compactors play a vital role in preparing surfaces for the various stages of construction projects. Whether ensuring stable soil for building foundations or achieving a smooth finish for pavement installations, choosing the correct compaction equipment can make or break a project. Compactors excel in tight spaces, while rollers provide efficient compaction over large areas. Understanding their diverse applications is critical to leveraging the best from each machine.
Road Construction and Maintenance
One of the most essential uses of rollers and compactors is in road works. During road building, rollers compact the sub-base and base course layers to provide an even and sturdy surface able to withstand heavy traffic loads. Their ability to achieve smooth, level compaction makes rollers especially suitable for asphalt paving.
Compactors are also important for trench compaction during drainage installation and compacting around underground utilities. Their maneuverability allows working in confined areas alongside a road. Regular maintenance activities like pothole repair and shoulder grading also require compaction, for which both machine types prove indispensable.
Preparing Land for Building Projects
Whether it be a housing complex, warehouse, or other structure, properly compacted soil is vital to the stability and longevity of buildings. During site preparation, rollers and compactors work to stabilize the ground. Their use results in an evenly compacted base supporting construction loads without settling issues.
This helps ensure buildings remain sturdy through their design life. Compactors’ smooth rollers especially come in handy for compacting around building edges and other limited access spots a roller cannot access. A firm soil foundation paved using compactors and rollers prevents costly structural issues in the future.
Landscaping and Pavement Installation
These construction applications also rely on efficient compaction. Roller use during landscaping creates a stable surface for amenities like pathways and parks. Their vibration assists with shifting drainage and irrigation lines into the ground. Compactors play a crucial role during hardscaping by preparing the ground for elements like retaining walls and ensuring a level base.
Both machine types are indispensable for installing concrete slabs and asphalt surfaces, where compaction achieves an even finish ready for use, whether residential or commercial; compactors and rollers form the groundwork of functional, long-lasting landscaping and pavement projects.
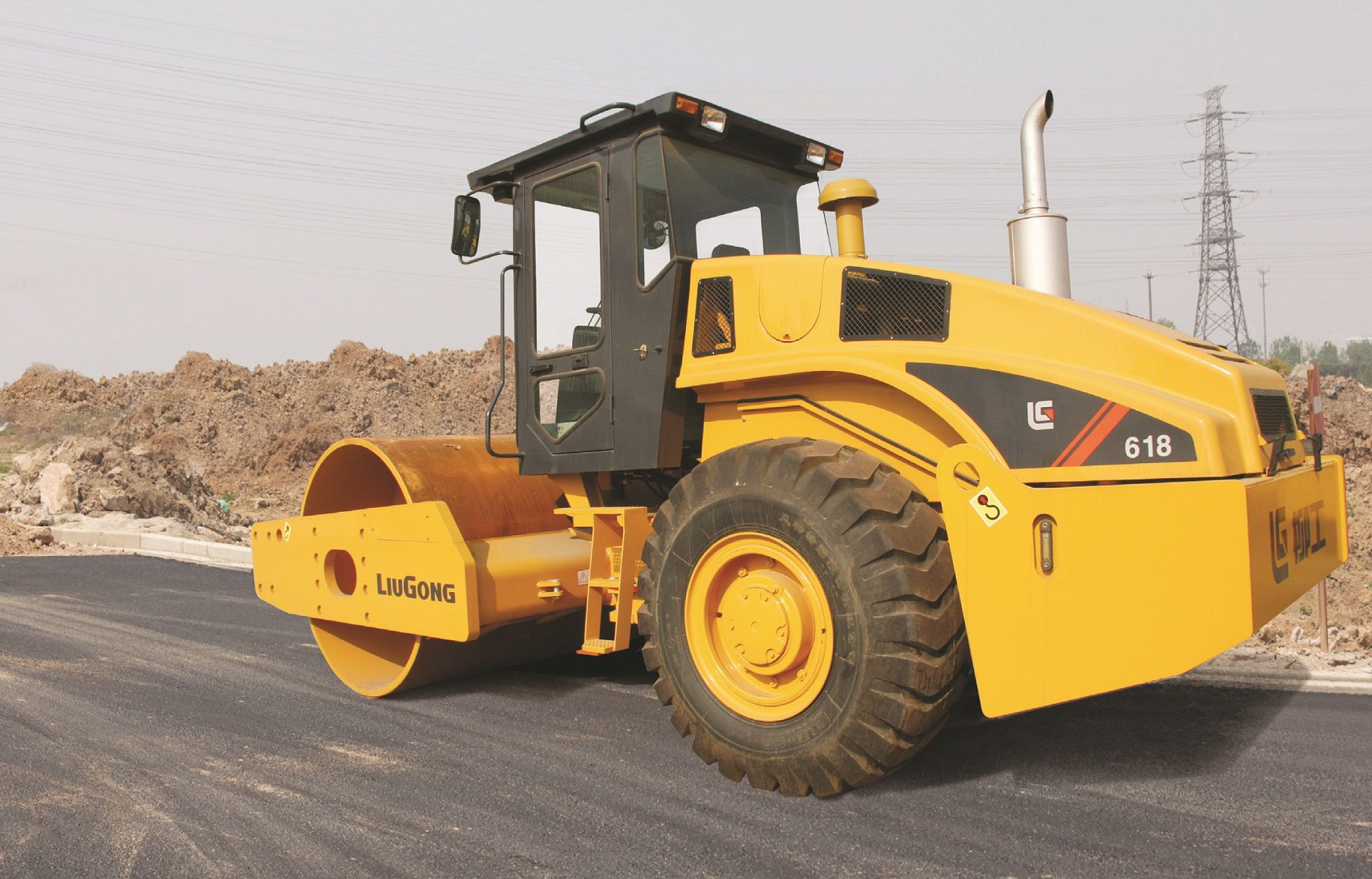
Factors to Consider When Selecting Equipment
There are several important factors to consider when selecting the right compaction equipment for a construction or landscaping project. Careful evaluation of these factors helps ensure the equipment chosen can efficiently and effectively complete the compaction requirements of the intended task.
Size of the Project Area
The size of the area needing to be compacted plays a crucial role in determining whether a roller or compactor is more suitable. Rollers are best for large, continuous project areas like road construction sites because they work faster over a wider coverage area. Compactors are better for smaller, irregular spaces that require precise maneuvering, such as walkways or trenches.
Type of Material Being Compacted
The type of material, such as soil, gravel, or asphalt, also influences equipment selection. For example, Padfoot rollers work well on cohesive soils to displace air and achieve dense compaction, while smooth drum rollers create a smooth, level finish when compacting granular materials. Plate compactors suit various other soil types and aggregate types in tight spaces.
Access and Terrain Conditions
Project terrain and access points must also be considered. Rollers are less maneuverable on steep slopes or confined areas that compactors can easily navigate. Compactors are well-suited to irregular surfaces and hard-to-reach places where larger equipment cannot fit or operate effectively. Rammer compactors are useful for trench compaction and other applications requiring precise control in limited spaces or uneven terrain.
By carefully evaluating the size, material type, and access conditions, contractors can determine whether a roller, compactor, or combination is most suitable to efficiently complete soil compaction, road construction, landscaping, and other tasks on schedule and within budget. This ensures the best possible outcome.
Choosing the Right Equipment for Soil Compaction
Proper soil compaction is essential for creating stable foundations for construction projects. The type of equipment used for soil compaction depends on the project scope and conditions.
Understanding the Compaction Process
There are always various layers and stages in any soil compaction process. Firstly, the surface layer is prepared by loosening the topsoil. Then, fill material like gravel or sand is added if needed. Compaction equipment is used to compress the soil in thin, uniform layers. This process is repeated for each added layer until the desired compaction level is achieved.
- Padfoot rollers are commonly used for compacting heavy clay soils that are difficult to work with. With its projections, the Padfoot design efficiently drives out air pockets and excess water from the soil.
- Smooth drum rollers are suitable for compacting granular materials like crushed stone or gravel, quickly displaced by excessive vibration. The smooth surface of the drum achieves compaction through static weight distribution without disturbing the material.
- Vibrating plate compactors are handy for compacting around obstacles or confined areas with restricted access. Their maneuverability allows compaction in trenches or along foundations where larger rollers cannot fit.
- Rammer compactors, called tamping rammers, deliver high-impact compaction through an oscillating foot pad, making them practical for rocky soils. The repeated pounding breaks up clumps and locks the material into a dense layer.
- Landfill compactors are applied where large volumes of waste must be compressed underground. Their durability and corrosion resistance allow them to withstand harsh conditions.
In conclusion, choosing the right compaction equipment depends on project needs, soil type, and site conditions. Combining different equipment helps achieve proper densities uniformly across the compaction area. This paves the way for stable constructions.