Road Roller Maintenance
Meta Description: Discover the importance of road roller maintenance for optimal performance & longevity. Learn essential maintenance tips & benefits for efficient operation.
Proper maintenance is crucial for road rollers used on construction sites. This article discusses the importance of routine maintenance tasks and inspections, developing a maintenance plan, critical focus areas, routine tasks, storage considerations, keeping records, and signs warrant professional servicing.
Following the recommendations can help operators keep their rollers running efficiently and minimize downtime.
Key Takeaways
- Perform daily cleaning, inspections, and lubrication to keep components functioning correctly.
- Develop a maintenance plan and follow manufacturer schedules to optimize performance.
- Focus on critical systems through routine tasks, such as drums, tires, fluids, filters, belts, and hoses.
- Ensure proper storage and operator training for maximum equipment life.
- Keep detailed maintenance records to track trends and schedule servicing appropriately.
- Outsource specialized repairs to certified technicians when needed to avoid costly downtime.
Understanding the Importance of Road Roller Maintenance
Proper road roller maintenance ensures the equipment functions appropriately on construction sites. Routine maintenance such as daily checks, cleaning the drum surface, ensuring correct fluid levels and lubrication of parts, inspecting filters, belts, and hoses, and replacing components as needed helps prevent issues from arising.
It keeps the roller, engine, hydraulic system, and other components operating efficiently so the machine can complete compaction work without downtime. Regular maintenance is critical to avoiding mechanical failures and unexpected repairs.
It’s essential to develop general solid maintenance practices, such as daily visual inspections, cleaning the drum and engine compartment, ensuring proper lubrication of parts, checking fluid levels and filters regularly, and performing other routine tasks. These help keep the roller functioning efficiently on job sites.
1. Developing a Maintenance Plan
Creating a maintenance plan that involves establishing a regular inspection schedule is critical. Daily checks of components like the hydraulic system, drum surface, hoses, belts, filters, fluid levels, and any leaks or issues help catch minor problems before they become more extensive repairs.
A set schedule for inspecting tires, drums, the water system, and other parts ensures thorough routine maintenance. Following the manufacturer’s recommendations for maintenance intervals and tasks also helps optimize the roller’s performance and longevity.
Establishing a Regular Inspection Schedule
Having operators perform quick daily maintenance checks of critical items like hydraulic oil levels inside the engine compartment, the condition of an air filter, and engine oil levels, as well as ensuring the parking brake and warning beacons are operating correctly, provides an opportunity to identify maintenance needs early on.
Weekly or monthly more in-depth inspections of the electrical controls, scraper system, spray nozzles, rubber mounts, and other components are allowed, allowing a deeper dive to check for loose wiring or worn parts and ensure components like the drum scrapers remain properly adjusted.
Following Manufacturer Recommendations
It’s essential to follow the maintenance schedule recommended by the road roller manufacturer to keep the equipment running efficiently. This involves:
- Check schedules for replacing engine belts, filters, hoses, and other parts to avoid mechanical failures.
- To properly lubricate components, refer to manuals for lubrication intervals and use the specified hydraulic oil, engine oil, and grease points.
- Following fluid change intervals for the hydraulic system, fuel tank, water tank, and drum to avoid build-up of dirt and other contaminants.
- Inspecting the drum surface, scraper system, spray nozzles, and rubber mounts at regular periods to maintain an efficient compaction process and avoid asphalt sticking on job sites.
- Ensuring maintenance tasks are performed after extended periods of heavy use or storage to check for issues like loose wiring and calcium deposits inside the water system filters.
2. Key Areas to Focus on to Maintain Optimal Performace
To maintain optimal performance, paying attention to specific components is essential. Thoroughly inspecting critical systems helps catch minor issues before they become costly repairs.
Inspecting Tires and Drums
The tires and drum are high-wear parts that require frequent checks. Inspect the tires for cuts, punctures, or uneven tread wear, which could cause instability. Examine the drum surface for signs of damage or build-up that may affect the compaction process. Scrape and clean the drum surface to avoid asphalt sticking on job sites.
Checking Fluid Levels and Filters
Routine maintenance involves checking fluid levels for the hydraulic system, fuel tank, water tank, and engine. Top up levels as needed and change fluids according to schedules.
Also, inspect air, fuel, and water system filters and replace them periodically to prevent contaminants from hindering the compaction equipment or hydraulic system’s functions. Check the condition of the hoses and belts, too.
Examining Belts, Chains and Other Components
Regular inspection and maintenance of additional components is essential:
- Check engine belts and hoses for cracks, wear, and proper tension to prevent breakdowns.
- Inspect rubber mounts, shock mounts, and other components for cracks, loose bolts, or leaks that could cause vibration issues.
- Examine hydraulic hoses and fittings for leaks affecting the hydraulic system function.
- Inspect safety features like backup alarms, warning beacons, and the parking brake to ensure they are clean, lubricated, and working properly.
- Check electrical controls and wiring for loose connections, corrosion, or damage to components such as the spray and scraper systems.
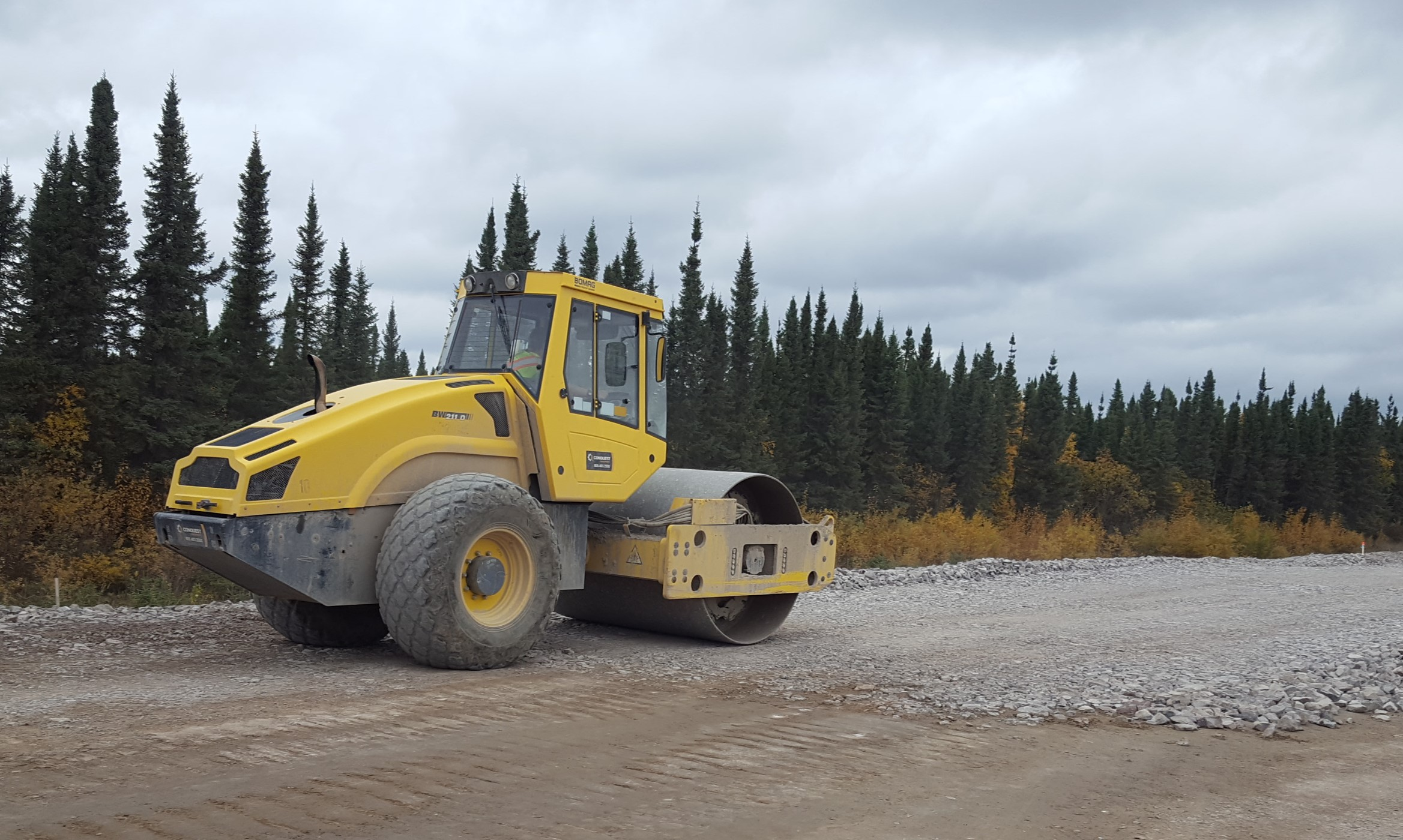
3. Routine Maintenance Tasks
Consistent performance of regular maintenance tasks is essential to keep the road roller running smoothly. Daily and weekly routines help prevent premature wear and failures.
Performing Daily Cleaning
Removing dirt and debris is crucial. Operators should clean the drum surface daily to avoid build-up that can cause asphalt to stick. They should also clean the engine compartment, spraying nozzles, and other areas to prevent overheating and ensure components like the spray system function properly. Using clean water and rags makes the cleaning efficient.
Conducting Lubrication
Proper lubrication is essential. Grease all grease points and inspect lubrication levels at least daily. Follow schedules for lubricating parts like the hydraulic system with the specified hydraulic oil. Careful lubrication reduces friction and wear, helping extend the roller’s service life. It also ensures movements like the drum scrapers operate smoothly.
4. Storage and Operational Considerations
How equipment is stored and operated can significantly impact its lifespan. Ensuring best practices are followed is essential.
Proper Storage When Not In Use
When a road roller is not in use for extended periods, it’s crucial to store it properly to prevent issues. Park it in a dry, sheltered area away from dirt and weather elements that could cause corrosion or leaks.
Drain fluids like fuel, hydraulic oil, and water from tanks to avoid the build-up of contaminants. Proper storage protects the machine’s condition.
Training Operators for Efficient Use
Thoroughly training roller operators leads to efficient operation and reduced maintenance needs. Educate them on daily checks, lubrication schedules, and detecting early signs of wear.
Training on safe operation helps prevent misuse that could damage components like electrical controls, scraper systems, or spray nozzles. It also ensures the compaction equipment functions properly to complete construction site jobs efficiently.
5. Keeping Maintenance Records
Documenting service history is essential for equipment management. Records provide valuable insight.
Benefits of Documentation
Thorough documentation of maintenance, repairs, and inspections is crucial. Keeping records of tasks performed, fluid changes, parts replaced, and any issues noted allows equipment managers to track the roller’s condition over time.
This helps identify maintenance trends and problematic components and determine appropriate service schedules.
Records also help comply with inspection standards for construction equipment. They provide proof that maintenance has been conducted, helping prevent liability issues. Detailed documentation thus benefits equipment performance and usability over the long run.
6. When to Consider Professional Servicing
While routine maintenance keeps a road roller functioning, it’s essential to outsource specialized servicing occasionally:
- Major overhauls or repairs to systems like the engine, hydraulic, or electrical systems may require professional expertise, specialized tools, and equipment unavailable on-site.
- Deeper servicing needs after an extended period of heavy use, such as cleaning built-up dirt inside water system filters, drum scrapers, spray nozzles, or replacing worn hoses and belts.
- Inspection and repairs for issues identified through maintenance records, such as recurring problems, leakage that cannot be fixed, or abnormal vibration requiring shock mount replacement.
- Emissions testing and any engine or hydraulic oil changes may need certification for compliance with construction equipment standards.
- Deep drum cleaning, repairs, or replacement of drum surface or scrapers for optimal compaction on job sites.
- Winterization, fluid flushing, or other storage-related servicing when putting a roller away for an extended period.
Maintenance Benefits For Road Roller
Here are some maintenance benefits for road rollers, including:
- Enhanced Performance: Regular maintenance ensures that the road roller functions properly, optimizing its performance on the job.
- Extended Lifespan: Proper upkeep, including visual inspection and ensuring proper lubrication, helps prolong the lifespan of the road roller.
- Efficient Operation: Monitoring and maintaining hydraulic oil levels inside the roller ensures smooth and efficient operation, reducing the risk of malfunctions.
- Clean Air Supply: Routine checks and replacement of air filters keep the air filtering system in top condition, providing clean air to the engine and enhancing its performance.
- Preventive Measures: Maintenance decals guide the roller operator in performing necessary tasks such as drum cleaning, adding fuel, and checking for loose water, preventing potential issues from arising.
- Safety Assurance: Regular maintenance ensures the road roller is functioning properly and reduces the risk of accidents on the job site, safeguarding the operator and bystanders.