Enhanced Connectivity And IOT Applications In Cranes
Meta Description: Discover how connectivity and IoT applications in cranes revolutionize operations, enhance safety, and optimize performance. Learn more about the benefits now.
IoT technology is enabling enhanced connectivity in cranes and material-handling equipment. This article discusses how leveraging IoT delivers significant benefits, such as improved safety, predictive maintenance, optimized operations, and real-time equipment insights.
Remote monitoring capabilities, automated protections, data-driven decision-making, and integrated management systems are transforming equipment management.
Key Takeaways
- IoT sensors continuously monitor equipment parameters, enabling remote operations for enhanced safety.
- Maintenance alerts optimize scheduling based on failure predictions from historical usage data.
- Automated protections immediately detect overloads or operator fatigue to prevent accidents.
- Insights into asset performance help identify efficient configurations and utilization periods.
- Integrated systems facilitate coordination across supply chains through real-time data exchange.
- Remote diagnostics expedite issue resolution to minimize costly downtimes.
How Enhanced Connectivity and IOT is Transforming Crane Operations
Integrating enhanced connectivity and IoT in cranes through dependable internet connectivity revolutionizes various industries such as construction.
Technologies like predictive maintenance, remote monitoring, and data analytics are helping crane operators and material handling equipment owners optimize resource allocation and streamline operations to achieve significant cost savings through ongoing operational improvements.
Real-Time Monitoring Through IoT Sensors
IoT sensors installed on cranes and other material handling equipment collect valuable data on parameters like load weight, boom angle, hydraulic pressure, fuel consumption, and environmental conditions.
This data is transmitted to cloud-based dashboards in real-time, allowing remote monitoring of equipment performance and health. Monitoring actual usage through IoT devices embedded in cranes helps identify periods of low utilization, aiding more accurate timing of preventive maintenance and resource allocation for maximum efficiency.
Remote control of cranes from safe distances is also now possible through dependable internet connectivity, enhancing safety on construction sites.
Remote Operation: A Game Changer for Safety
Technological advancements in IoT and connectivity have enabled remote monitoring and control of cranes and other equipment. This represents a significant shift that is enhancing safety across various industries.
Operating From Safe Distances
Dependable internet connectivity allows crane operators to control lifting equipment from ground level or another safe location away from overhead hazards. This helps protect key personnel on high-risk construction sites.
Remote operation facilitates work in dangerous areas, such as near power lines or crowded job sites, with a higher risk of accidents. Operators can maneuver cranes safely without exposure to live wires or other hazards.
The remote control also helps crane operators work safely in harsh environments like high winds or severe weather conditions that otherwise compromise safety. IoT devices provide real-time data on parameters like load weight, boom angle, and environmental conditions to guide operations securely.
Leveraging IoT and connectivity solutions, a single operator can remotely manage multiple cranes simultaneously from a centralized control room. This centralized monitoring and control improves safety supervision on large industrial sites and facilities with multiple lifting equipments.
Working in Harsh Environments
IoT sensors installed on cranes and other material handling equipment can provide operators real-time data on load weight, boom angle, environmental conditions, and fault status. This enables remote control of such equipment even in harsh weather conditions like high winds or severe storms.
Leveraging IoT connectivity, crane operators can now maneuver lifting devices securely from a safe distance without exposing themselves to potential hazards. IoT devices collect data on variables like fuel consumption, energy usage, and amperage ranges to guide efficient, dependable, and safe operations across varying weather events.
Predictive Maintenance for Improved Uptime
Leveraging IoT technology for predictive and preventive maintenance helps material handling equipment owners optimize uptime and reduce operational costs. Real-time component monitoring and data-driven failure predictions improve safety and efficiency.
IoT Sensors for Component Condition Monitoring
IoT sensors embedded in cranes, overhead handling equipment, and other machinery continuously collect fault codes, vibration data, and other parameters. This valuable equipment data is transmitted to cloud dashboards for analysis. Monitoring trends helps identify maintenance needs before failures occur.
Data Analytics for Predicting Failures
Machine learning algorithms can analyze historical maintenance data, usage patterns, and sensor readings from interconnected IoT devices. This facilitates predictive analytics that identify when specific parts may degrade past a pre-determined threshold.
Maintenance teams can then proactively replace components and minimize downtime, achieving significant cost savings compared to reactive repairs. Regular data exchange between the equipment and the cloud keeps predictions accurate using the latest operational insights.
Enhanced Safety with Automated Protections
IoT technology helps introduce several automated safety measures for cranes and material handling equipment. Remote alerts and shutdowns based on real-time data minimize risks.
Detecting Overloads and Imbalances
Sensors in lifting machinery monitor operational parameters like load weight, boom position, and variable frequency drives. They can instantly detect unsafe overload conditions or mechanical imbalances.
The system triggers visual/audio alerts on remote operator consoles, apps, and dashboards. IoT devices are programmed to initiate controlled descent or shutdown sequences to prevent accidents in emergencies.
Monitoring Operator Fatigue and Alerts
Collecting biometric data through wearable IoT devices can monitor crane operators’ fatigue and distraction levels. If the data crosses a pre-determined threshold, automated alerts are dispatched to supervisors, indicating reduced alertness, automated alerts are dispatched to supervisors.
For enhanced safety, supervisors can then schedule breaks or replace operators as a precautionary measure before accidents occur. Such safety measures are essential for job sites and shifts extending late into hours.
Optimizing Operations Through Data Insights
Leveraging valuable data collected from IoT sensors allows crane operators and equipment owners to streamline operations for improved efficiency.
Identifying Periods of Low Utilization
IoT devices track the actual usage parameters of cranes and material handling machines in real-time, including operating hours, energy consumption, and fault logs.
- When analyzed with machine learning, this operational data reveals periods of low activity across variable shifts, seasons, or job functions.
- Such insights help optimize resource allocation and schedule preventive maintenance during lean periods to minimize disruption to high-productivity seasons.
- Identifying underutilized equipment also aids in better distribution of workloads to achieve maximum output from existing assets.
Overall, these data-driven decisions facilitate ongoing operational efficiency and cost savings improvements.
Determining Efficient Configurations
By analyzing valuable historical data collected from IoT sensors on multiple job sites, crane operators and material handling companies can identify the most efficient equipment configurations and setups for specific tasks.
Machine learning algorithms leverage parameters like energy consumption, operating hours, payload data, and fault logs to determine optimal equipment sizing, attachments, and setups matching each application.
This helps maximize productivity from existing assets while minimizing operational costs through improved efficiency and resource allocation. Data-driven insights also facilitate ongoing enhancements in safety, performance, and cost savings.
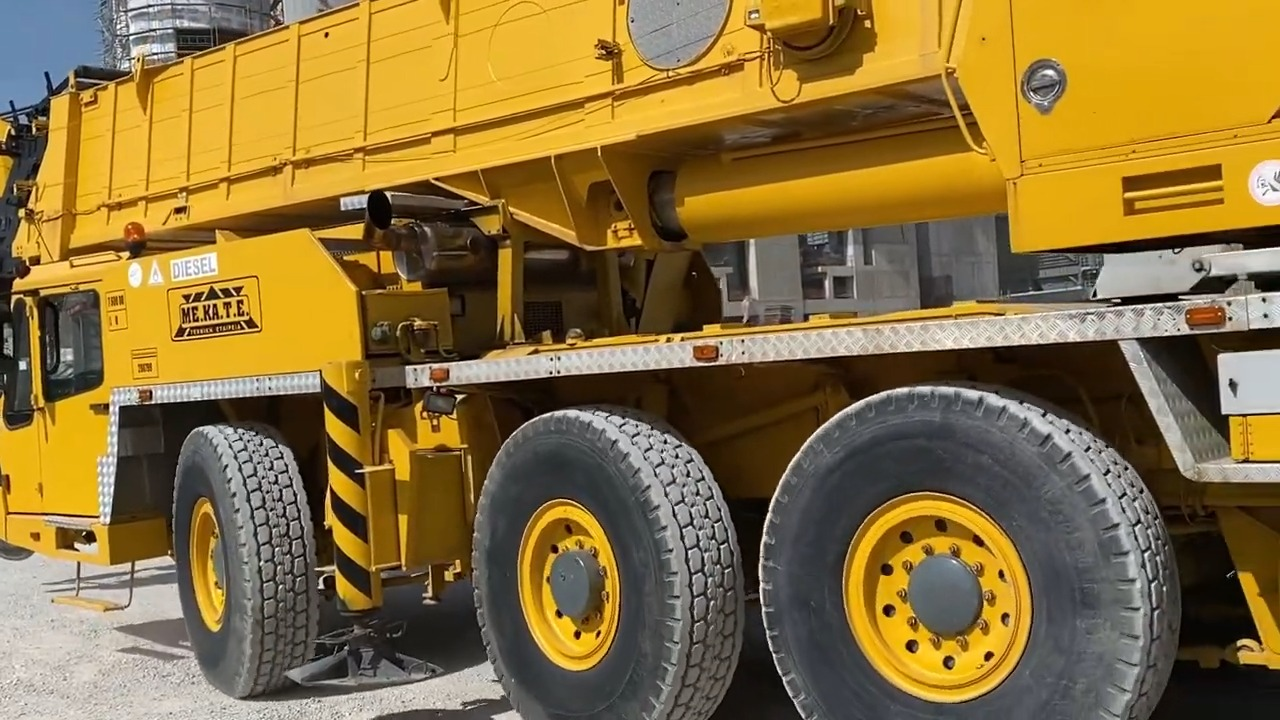
Integrated Management Systems for Coordination
Seamless integration of IoT solutions with other digital tools facilitates coordinated operations for enhanced efficiency.
Connecting to Project Planning Tools
Real-time equipment data collected from IoT sensors can be exchanged with project management software systems. This automatically updates crane availability and maintenance schedules into master project plans.
In turn, planned lifts and timelines from construction management tools feed into crane operator dashboards. Seamless data exchange between these interconnected devices ensures all key personnel access consistent and accurate information.
It also helps optimize the coordination of equipment, crews, and supplies across the supply chain, enabling just-in-time project execution within deadlines and budgets.
Interfacing with Inventory Systems
IoT sensors on cranes and other material handling equipment can track usage data of spare parts in real-time.
- When integrated with inventory management software, this valuable data facilitates just-in-time reordering.
- Automatic replenishment ensures the availability of critical components, avoiding production delays due to stockouts.
- The two-way exchange of equipment health insights and stock levels between interconnected IoT devices and inventory systems optimizes resource allocation.
- It helps achieve cost savings through reduced overstocking and faster turnarounds on maintenance needs identified via predictive analytics of operational data.
Overall, seamless data integration delivers improved visibility and coordination across supply chain operations for enhanced efficiency.
Remote Diagnostics for Rapid Issue Resolution
Leveraging IoT enables remote diagnostics that help resolve equipment issues quickly:
- IoT sensors continuously monitor operational parameters and transmit real-time fault codes/error messages.
- Technicians can remotely access this stream of equipment data through cloud dashboards for rapid troubleshooting.
- Using fault pattern analysis and machine learning, they can identify root causes before on-site inspection.
- Remote code downloads facilitate immediate fixes via software/firmware updates without physical access to machines.
- Spare parts can be pre-configured for replacement based on predictive failure alerts to minimize downtime.
- Event-based notifications keep key personnel updated on equipment health for a coordinated response.
Overall, IoT-enabled remote diagnostics significantly reduce downtimes and associated costs through faster issue resolution.
Benefits Of Enhanced Connectivity and IOT Technology in Cranes
Remote monitoring and control capabilities improve safety on high-risk construction sites by enabling operators to work from safe distances. IoT sensors provide real-time visibility of equipment operations.
Using data from embedded IoT devices, predictive maintenance helps material handling equipment owners optimize equipment uptime and reduce unexpected downtime through more accurate repair and replacement scheduling.
It has automated safety features that detect overloads, fatigue, and environmental hazards that safeguard operators, personnel, and machinery. Remote alerts enable instant corrective actions to be initiated.
Data-driven insights into asset usage and performance help crane operators and owners optimize resource allocation, streamline operations, and minimize operational costs through ongoing improvements.
Integrating IoT data with project planning tools and inventory systems facilitates coordinated operations across supply chains, enabling just-in-time project execution.
Remote diagnostics using fault codes and patterns transmitted from IoT devices expedite issue resolution, lowering downtimes and associated costs through faster response.