real-time-diagnostics-for-cranes
Meta Description: Discover how real-time crane diagnostics ensure safety, maximize uptime, and streamline maintenance, utilizing advanced technologies and predictive analytics for optimal performance.
Real-time diagnostics for cranes play a crucial role in modern crane management. Monitoring equipment health through sensors and data analytics can identify potential issues early. This allows for proactive maintenance planning to optimize safety, uptime, and efficiency.
This article discusses real-time monitoring technologies and how their integrated use enables improved maintenance practices for safer and more productive crane operations.
Key Takeaways
- Real-time diagnostics leverage sensors, data analytics, and remote monitoring to proactively detect crane issues through continuous equipment performance monitoring.
- Predictive analytics of operating parameters help schedule optimized preventive maintenance to maximize safety and uptime while minimizing downtime costs.
- An integrated approach analyzing usage insights aids decision-making for improvements in areas like operator training and maintenance planning for enhanced overall crane operations.
Understanding The Diagnostics For Cranes
Real-time diagnostics for cranes leverages continuous vibration monitoring systems and technology-based monitoring programs featuring wireless communication technologies to collect and analyze relevant operating data from cranes equipped with vibration sensors and monitoring installations.
Condition monitoring practices analyze vibration data and predictive maintenance through diagnostics systems to help provide a complete overview of crane components’ machine condition for preventative maintenance and minimizing downtime.
The Importance of Real-Time Crane Monitoring
Real-time crane diagnostics through continuous vibration monitoring systems and condition monitoring practices are crucial for critical crane applications. Technology-based monitoring programs leveraging wireless communication technologies and data storage capabilities provide a complete overview of crane components’ machine condition.
- Ensuring Safety in Crane Operations: Real-time diagnostics systems monitoring vibration data and relevant operating data can identify issues early using vibration analysis. This helps prevent potential failures in hoist units, ropes, and other equipment, thus ensuring safety in crane operations.
- Maximizing Crane Uptime and Productivity: Collecting operating parameters through monitoring a crane installation and predictive maintenance solutions helps schedule preventative maintenance, reducing downtime from unexpected failures. Remote monitoring from mobile devices also allows quick resolution of issues, maximizing crane uptime and productivity.
- Reducing Unplanned Maintenance Costs: Condition monitoring practices and diagnostic purposes can assess machine conditions and monitor remaining service life. This helps plan maintenance for optimal operational efficiency. It also reduces unplanned maintenance costs by minimizing downtime through preventive maintenance based on vibration and other data trends.
A Deeper Look at Real-Time Crane Diagnostics Technologies
Real-time crane diagnostics leverage various monitoring systems and technologies to provide a complete overview of operating reliability. Not all monitoring systems can handle the same fundamental challenges cranes face in critical applications.
- Sensor Technology for Performance Monitoring: Continuous vibration monitoring systems with sensors collect vibration and relevant operating data from crane components. Technologies like gear mesh frequency monitoring help detect anomalies in gear systems and other equipment, enabling predictive maintenance.
- Advanced-Data Analytics for Anomaly Detection: Monitoring installations featuring wireless communication technologies transmit data to computer processing systems. Condition monitoring software then analyzes data records using vibration analysis and comparative data to identify issues. This advanced data analytics helps detect anomalies for preventative maintenance.
- Predictive Maintenance through Condition Monitoring: Diagnostics systems monitor machine condition indicators like remaining service life. When drops in things like hoist units and rope hoist data are detected, predictive maintenance solutions can schedule repairs before potential failures. This minimizes downtime through condition monitoring practices.
Remote Diagnostics for Improved Issue Resolution
Remote monitoring through convenient remote diagnostics provides complete oversight of operating status. The demag status control system offers mobile device-based monitoring for multiple cranes.
This enables experts to access collected data and identify issues remotely. By leveraging wireless communication technologies, repairs can be guided remotely. This reduces downtime through minimizing downtime by resolving issues quickly from any location.
Data-Driven Insights for Optimizing Crane Operations
Real-time diagnostics generate vast amounts of relevant operating data through monitoring installations—condition monitoring practices and predictive maintenance extract valuable insights from this data.
Software with intuitive interfaces helps analyze usage patterns, component wear, and operator efficiency. This comparative data aids asset management and capital fund allocation decisions. It also identifies optimization opportunities, such as training needs, to improve operational efficiency.
Integrated Maintenance Management for Planning
Real-time diagnostics systems generate vast amounts of relevant operating data that can be used for integrated maintenance planning when connected to maintenance management software. Condition monitoring practices leverage this data to schedule preventative maintenance activities like:
- Generating status reports on machine condition indicators to plan repairs and replacement of crane components like hoist units before remaining service life drops
- Establishing pre-defined threshold values for vibration levels and other parameters to trigger maintenance alerts
- Producing spare parts lists and requirements based on usage to streamline inventory management and minimize downtime from component failures
- Providing a complete overview of the operating reliability of multiple cranes and industrial applications to aid capital funding allocation decisions
By integrating monitoring installations and diagnostic purposes data with maintenance management software, companies can save time and cost through more efficient preventative maintenance planning.
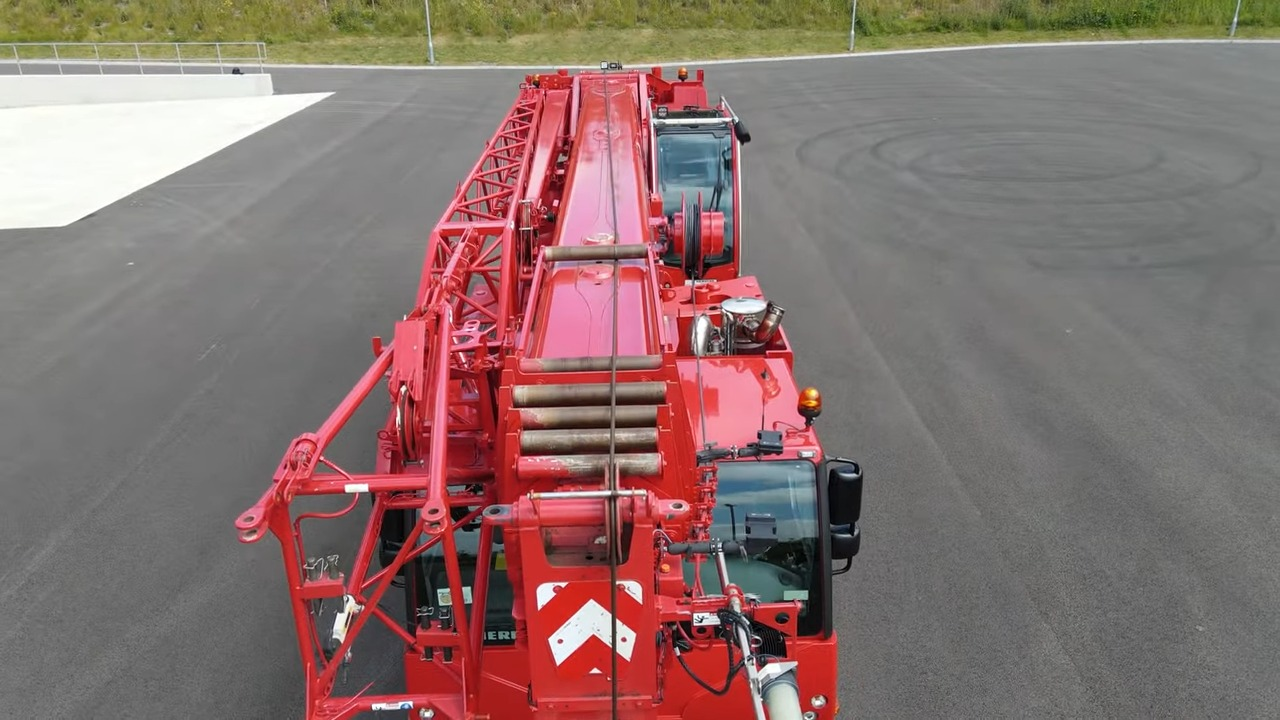
Advantages Of Real-Time Diagnostics For Cranes
Ensures safety in critical crane applications by enabling early detection of potential failures in crane components like hoist units through continuous vibration monitoring systems.
Maximizes crane uptime and operational efficiency by facilitating preventative maintenance through predictive vibration analytics and other relevant operating data collected from monitoring installations.
Reduces unplanned downtime and associated costs through condition monitoring practices that monitor machine condition indicators and schedule repairs/replacements before the remaining service life drops significantly.
Provides a complete overview of performance across multiple cranes and industrial applications to aid capital funding allocation decisions for optimized asset management.
Streamlines inventory management and minimizes downtime through integrated maintenance planning leveraging data from diagnostics systems and status reports on crane components.
It allows remote troubleshooting and repairs through convenient remote monitoring technologies, like the Demag StatusControl system, for quick issue resolution from any location via mobile devices.