Troubleshooting and Repair Techniques For Cranes
Meta Description: Discover essential troubleshooting and repair techniques for cranes, ensuring safety and efficiency. Learn how to address electrical and mechanical issues to maintain optimal performance.
Proper maintenance and effective repairs are essential to ensure the reliable performance of cranes over time. This article discusses critical aspects technicians must consider when troubleshooting issues and performing repairs to restore cranes to safe and optimal working order.
The various steps, techniques, and safety precautions outlined here provide a comprehensive guide for crane service professionals. So, without getting into any additional details, let’s head away.
Key Takeaways
- Follow a logical troubleshooting process starting with inspections and functional testing.
- Leverage diagnostic tools to measure parameters for pinpointing issues precisely.
- Review maintenance records for recurring faults or gaps needing to be addressed.
- Employ replacement of broken parts and adjustments to optimize performance.
- Ensure repairs follow safety protocols with proper equipment and certified staff.
Importance of Proper Troubleshooting and Repair
Proper troubleshooting and repair techniques are essential for cranes to ensure safety, reliability, and efficiency.
It is essential to systematically identify root causes by eliminating and inspecting components like the motor, contactor, and brake for issues like oil leakage, wiring errors, or contact pressure problems. Only qualified technicians should perform repairs to eliminate failures and maintain rated performance.
Key Steps in the Troubleshooting Process For Cranes
Proper troubleshooting of cranes requires systematically identifying issues through a logical sequence of steps. Narrowing down failures by thoroughly checking various components and parameters using established methods is important. This includes carefully:
Performing a Thorough Visual Inspection
- Inspect all crane components, such as the motor, contactor, brake, and wiring, for issues such as oil leakage, contact pressure problems, or wiring errors.
- Examine the rope diameter working surface and for any mechanical impurities.
- Check for abnormalities in the rotor, like deformation, and issues in the bearing, like wear or damage.
- Inspect the controller handle, reducer shaft, and other mechanical parts for signs of failure.
- Look for problems in the connections, like loose or bad contact points.
- Carefully observe the fixed and moving contacts in the contactor for pitting or burning.
Conducting Functional Tests
Functional testing helps identify malfunctions like motor or brake failures through operation. The crane is put through full lifts and slews while monitoring parameters such as current, voltage, speed, and load for any deviations from rated values that could point to electrical, mechanical, or hydraulic issues needing repair or component replacement.
Leveraging Diagnostic Tools
Diagnostic tools are essential aids that precisely measure vital inputs and outputs and detect subtle changes indicating problems. Specialized software and meters diagnose the control system, monitor pressure and flux in hoses and circuits, measure bearing vibration levels, and listen for abnormal sounds.
This precision diagnostic data helps narrow down faults needing corrective maintenance or remediation, like adjusting contact pressure or replacing worn parts.
Reviewing Maintenance Records
- Inspect logs for any overdue maintenance or component replacements like bearing lubrication or slip ring cleaning
- Check if repairs were performed as per OEM manual or industry best practices
- Note if qualified technicians completed tasks or if repairs were done correctly
- Review records for recurring issues that were not adequately eliminated, like contact wear or voltage problems
- Look for gaps or missed maintenance that could lead to failures in the motor, brake, or hydraulic systems
- Ensure all work was done as per design parameters and essential tips to avoid future faults
By thoroughly reviewing past maintenance and repair records, technicians can gain valuable insights for troubleshooting current issues and identify any defects in the maintenance process for continuous improvement.
Common Cranes Issues That Require Repair
Many issues can develop over time and use that require repair work on cranes. Two primary categories of faults include mechanical wear problems and electrical system issues. Addressing these common conditions is important for reliability and safety.
Mechanical Component Wear and Damage
Components like motors, brakes, ropes, bearings, and other moving parts are susceptible to degradation from friction, abrasion, corrosion, and overloading.
Issues like bearing wear, reducer shaft damage, rope deterioration, or contact surface pitting must be repaired by replacing worn parts or reconditioning worn surfaces.
Electrical System Faults
Cranes use complex electrical control and power systems that can develop problems. Troubleshooting is needed to fix faults in the wiring, contactor, slip ring, or other components.
Issues involving voltage drops, short circuits, relay failures, or loose connections require repairing or adjusting the motor, controller, or other electrical systems according to the design parameters.
Hydraulic System Leaks or Malfunctions
- Check for oil leaks in hoses, pipes, pumps, and cylinders caused by wear and tear
- Inspect hydraulic components like valves, motors, and filters for damage or clogging
- Test the hydraulic circuit for pressure regulation issues, leaks at connections or couplings
- Monitor for malfunctions in lowering, lifting, and braking caused by faults in the hydraulic control system
- Address hydraulic fluid contamination or depletion below rated levels through cleaning and refilling
- Repair hydraulic system malfunctions per design parameters to ensure full-speed operation and braking time
- Replace worn or damaged hydraulic components like seals, hoses, and pumps to restore function
Proper troubleshooting and timely repairs are necessary to maintain performance and safety by fixing common hydraulic issues by replacing faulty parts or reconditioning components.
Effective Repair Techniques For Cranes
Technicians employ tried and tested repair methods to restore cranes to proper working order. These include replacement of damaged components as well as adjustments to optimize function.
Replacing Broken or Worn Parts
Replacing mechanical parts that are broken, worn, or damaged beyond repair is crucial. Slip rings, bearings, contractors, and other worn components are replaced using OEM or equivalent parts to rated specifications. This ensures full-rated performance and reliability.
Adjusting Settings for Optimal Performance
Technicians also carefully adjust settings like contact pressure, voltage levels, pump pressures, and speeds to stay within design parameters. Fine-tuning configurations eliminate issues like loose connections, slip rings, or under-voltage that lead to failures. Adjustments optimize operation for rated loads at full speed.
Applying Lubricants to Moving Parts
Proper lubrication of moving components is essential to repair cranes and restore rated performance. Technicians must carefully:
- Grease bearings, shafts, gears, and other parts using the lubricants specified in manuals
- Lubricate slip rings, contact surfaces, and other current-carrying components to reduce friction and wear
- Apply lubrication to all parts subjected to pressure, tension, or abrasion from movement like ropes, linkages, and hydraulic cylinders
- Re-lubricate components based on hours of operation or maintenance schedules for prevention of failures
- Use lubricants suited for the ambient temperatures and working conditions faced by the crane
- Inspect lubricated parts regularly to ensure adequate lubrication levels are maintained per design parameters
Technicians can minimize abnormal sounds and bearing damage from metal-to-metal contact over time by thoroughly cleaning and applying the correct grade and amount of lubricants.
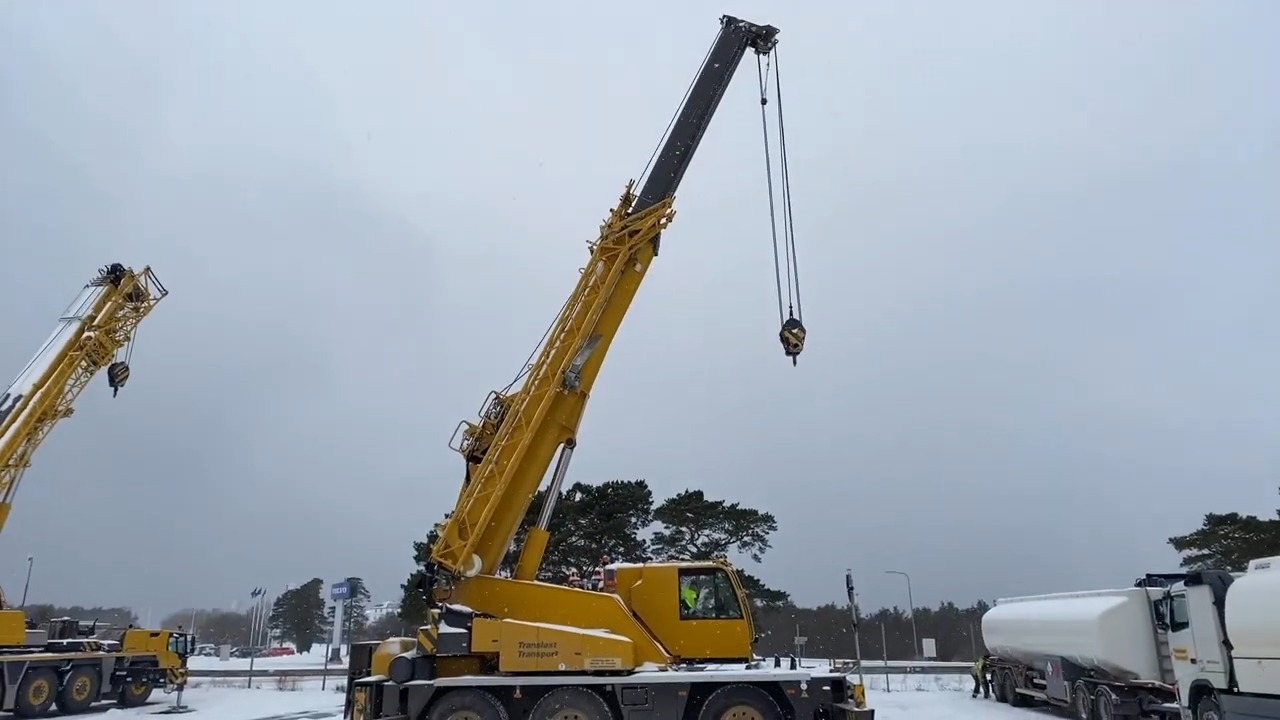
Ensuring Crane Repairs are Done Safely and Correctly
Safety is paramount when repairing cranes to prevent injuries. Technicians must follow strict protocols.
Using Proper Safety Equipment and Precautions
Repair work requires appropriate safety gear:
- Wear protective clothing, gloves, and steel-toed boots at all times near moving components
- Use insulated tools and safety glasses when working on electrical systems
- Utilize fall protection like harnesses and railings for high-elevation maintenance
- Properly secure cranes before repairs and tag out energy sources like compressed air lines
- Refer to lock-out/tag-out procedures for repairing energized equipment per important tips
- Never bypass or turn off safety devices – do repairs with full guarding of pinch points
Technicians can eliminate potential hazards during crane repairs by strictly employing safety practices.
Employing Trained and Certified Technicians
It is crucial to eliminate potential hazards by ensuring only qualified repair personnel work on cranes. Technicians must be trained on crane components, systems, essential tips, and approved repair methods.
They should understand troubleshooting techniques and electrical and mechanical maintenance requirements per industry standards. Certification demonstrates that technicians have the skills to correctly identify and resolve issues according to design parameters while following strict safety protocols.
Using certified professionals trained in crane repair helps ensure repairs are performed efficiently without the risk of future failures or injuries.