Construction Equipment Management Guide
Meta Description: Optimizing construction equipment management is crucial for project success. Learn about equipment acquisition, maintenance, safety, and more. Maximize asset lifespan and productivity.
Construction equipment management is vital for contractors to complete projects on time and budget. This article provides an overview of best practices for monitoring, maintaining, and allocating construction machinery and heavy tools.
By following the guidelines discussed here, equipment managers can maximize the lifespan of their assets and ensure non-stop productivity at job sites. Proper planning and care of the equipment fleet can help reduce costs and improve overall performance.
Key Takeaways:
- Construction equipment plays a vital role in project success and contractor performance.
- The construction equipment manager oversees job site machinery, tools, and heavy assets.
- Renting equipment can help reduce initial costs for contractors.
- Proper management ensures efficient equipment usage and maximizes asset lifespan.
What is Construction Equipment Management?
Construction equipment management oversees all machinery, tools, and heavy assets used at construction sites. It is the process of directing, monitoring, and controlling all equipment contractors use in the industry.
This includes tasks like tracking detailed records of each piece of equipment, planning preventative maintenance schedules and routine inspections, assessing utilization reports, managing fleet storage and security, coordinating transportation to and from job sites, properly training operators, and ensuring the right equipment types and capacity are used for each construction project and task.
Equipment managers are responsible for the entire equipment management process, which impacts project delays, costs, and construction companies’ overall performance and success.
Why is Construction Equipment Management Important?
Effective construction equipment management is crucial for any contractor as it can significantly reduce risks and costs associated with equipment damage, repairs, and downtime while maximizing productivity at job sites.
When appropriately implemented through a systematic management system and strategies, it helps address challenges like unexpected breakdowns and theft. This ensures projects are completed on time and budget without delays. It also leads to better industry practices and returns on all equipment investments in the long run.
Proper management allows efficient equipment requests and rental options for each construction project’s needs. It extends the lifespan of assets through preventative maintenance, inspections, and properly trained operators handling machinery safely according to practices.
Choosing the Right Equipment Management
Choosing the appropriate construction equipment is an important part of the management process that impacts project success. Proper evaluation of needs and conditions helps ensure the most effective equipment types are utilized.
Evaluating your project needs
It is crucial for equipment managers to thoroughly assess the specific requirements and tasks of each construction project. This includes reviewing the scope of work documents, budgets, timelines, and similar past projects to determine what machinery, tools, and assets will best complete the job on schedule and budget.
Fully understanding the project needs allows for proper equipment requests, rental options, and investments in line with each project’s specifications.
Considering site conditions
Carefully evaluating the location, terrain, and climate where the project will take place is also essential when selecting equipment. The location presents transportation challenges, while conditions may impact productivity and maintenance needs.
Managers must account for space constraints or environmental factors like dust, moisture, or temperature extremes. This ensures that the equipment has the capacity and durability suited to the job site conditions.
Setting your budget
Determining the construction project’s equipment budget is another essential step in selecting the right machinery. Budget constraints will directly impact the available equipment options and investments.
Thoroughly assessing costs like transportation, maintenance schedules, operating expenses, and potential repairs helps ensure budget accuracy when making equipment decisions. This allows contractors to request resources and rentals appropriately based on financial limitations.
Researching equipment suppliers
Evaluating reputable equipment suppliers in the local area is also crucial. Finding providers that offer the required machinery, tools, and assets within budget and for the necessary period ensures projects stay on schedule.
Suppliers should fit the job site location needs regarding transportation and provide quality equipment suited to potential site conditions. Reviewing warranties, safety records, and past client feedback helps construction companies make well-informed choices aligned with their project specifications, budgets, and timelines.
Maintaining Your Equipment Management
Effective maintenance is crucial for construction equipment management and maximizing asset lifespan. Keeping machinery properly serviced reduces downtime and repair costs over the long run.
Developing maintenance procedures
It is essential to establish standardized processes for addressing equipment needs. Documenting maintenance schedules, inspection checklists, and repair guidelines aligned with manufacturer recommendations ensures consistent preventative care.
This includes routine service tasks as well as protocols for unexpected issues. Construction managers can then properly plan maintenance timelines, budgets, and resource requirements according to the developed procedures.
Performing regular inspections
Thorough inspections allow early detection of potential problems before they cause serious delays or damage. Inspecting equipment inside and out regularly according to the maintenance procedures helps identify signs of wear.
This may include checking fluid levels, lights, brakes, and more. Inspections can be done before each use and as part of routine service. Recording inspection results helps track maintenance history and asset condition over time for replacement planning.
Maintaining equipment records
Keeping comprehensive documentation is crucial for effective construction equipment management. Detailed records provide visibility into maintenance needs and asset history over time. Equipment managers should log all services, repairs, operating hours, and other milestones.
This includes inspection results, preventative maintenance performed, and any issues addressed. Maintaining digital records in a cloud-based software system allows easy access for planning and sharing information across job sites.
Contractors can then track the lifespan return on maintenance investments for each piece of equipment. Detailed records support replacement planning, warranty claims, and resale or liquidation assessments.
Training Your Operators
Providing properly trained operators is crucial for effective construction equipment management. It helps maximize asset lifespan and productivity.
Assessing training needs
Regular performance evaluations using data from equipment management software and detailed records identify knowledge gaps. Monitoring utilization reports provides insight into priority training needs based on experience levels and certifications.
Delivering effective training programs
Initial and refresher courses should be developed using a combination of classroom, virtual, and hands-on methods to accommodate different learning styles. Training programs must cover machine-specific functions, safety protocols, maintenance responsibilities, and best practices aligned with manufacturer recommendations.
Providing ongoing coaching
In-field coaching and mentoring reinforce safe operation skills and address issues as they arise through continuous support. This helps operators maintain certifications and optimize performance over the long term to complete tasks efficiently.
Addressing training requirements through well-structured programs and routine coaching ensures operators extend equipment life on construction projects.
Proper operator instruction is integral to construction equipment management success through needs assessment, training program development, and ongoing development. It reduces risks, costs, and delays for construction companies.
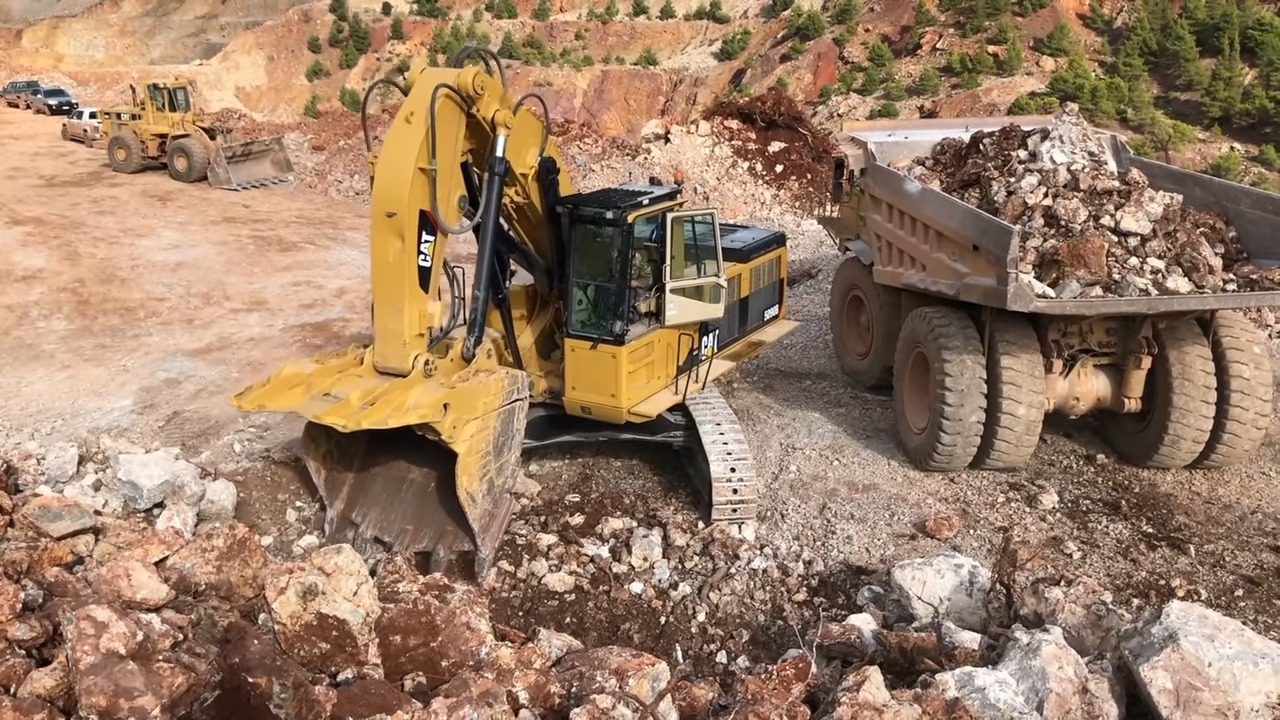
Monitoring Equipment Performance
Close performance monitoring is key to effective construction equipment management. It helps optimize resources and reduce unexpected costs.
Tracking equipment usage
Utilizing an equipment management system with cloud-based software allows real-time visibility into fleet utilization across all job sites. Equipment managers can track each asset’s operating hours, fuel usage, and maintenance records.
This usage data provides insight into peak/off seasons and highest/lowest producing machines. Analyzing reports helps identify underutilized equipment for potential consolidation or updating maintenance schedules as needed based on hours of use.
Equipment managers can also use usage tracking to refine rental and replacement plans long-term.
Analyzing maintenance vs repair costs
Reviewing detailed records like maintenance logs and expenses compared to repair bills helps determine where to focus improvement efforts.
Assessing which equipment demands the highest operating and repair costs per hour highlights areas for training, specification changes, or the need for upgrades. This performance analysis allows contractors to minimize unnecessary expenditures and maximize returns on maintenance investments over time.
Planning for Downtime and Replacements
Anticipating equipment downtime and replacements is an important part of construction equipment management. Proper planning ensures projects face fewer delays and costs.
Preparing contingency plans
Unexpected breakdowns will inevitably occur, so equipment managers should develop contingency plans. Maintaining a short-term rental program allows swapping assets if needed. Establishing maintenance schedules that anticipate seasonal demands prevents downtime.
Memorandums of understanding with equipment suppliers guarantee timely repairs or short-term loans if issues arise. Developing detailed plans that leverage utilization reports and maintenance histories prepares contractors for potential disruptions.
Evaluating replacement needs
Equipment managers can track machine hours, repair costs, age, and condition to project remaining lifespans. Comparing the costs of continued repairs versus replacement options helps determine the most economical decisions. Replacing equipment before failures occur avoids costly delays.
Budgeting for replacements according to detailed plans ensures contractors have the necessary resources and rental support available.
Preparation considering utilization data, maintenance records, and potential replacement timelines better positions contractors to avoid project delays from unforeseen issues or normal equipment cycles.
Ensuring Safety on Jobsites
Safety should be the top priority in construction equipment management to prevent injuries and liability issues.
Establishing safety protocols
Equipment managers develop comprehensive safety protocols for each machine according to manufacturer specifications, regulatory standards, and past incident analyses. Procedures cover operating procedures, inspection checklists, hazard assessments, and emergency plans.
Thorough safety training programs and ongoing coaching ensure protocols are followed consistently across all job sites.
Providing protective equipment
Contractors must properly equip operators for safe operation and unforeseen situations. This includes personal protective equipment like steel-toed boots, gloves, and ear/eye protection tailored to each machine’s functions.
Regularly inspecting PPE conditions prevents safety issues. Emergency equipment like fire extinguishers and first aid kits stored on job sites address unexpected incidents promptly to minimize impacts.