Long Term Investment Planning For Construction Equipment
Meta Description: The comprehensive guide to long-term investment planning for construction equipment. Explore factors, financial analysis, and sustainability considerations.
This guide will help construction business owners understand the key long-term equipment investment planning factors. It examines the types of machinery required and the costs involved at each stage of ownership.
The article analyzes options like purchasing, leasing, and renting equipment while providing tips on budgeting, financing, and maintaining equipment over extended project timelines.
Key Takeaways:
- Properly assess total ownership costs, including maintenance over the equipment’s useful life, to identify the most cost-effective solution long-term.
- Employ analytical tools like IRR, payback period, and risk assessment to make informed investment choices aligned with a construction business’s financial capabilities.
- Consider future trends and evolving industry regulations to optimize long-term planning and future-proof investments.
- Evaluate sustainable best practices and lower emission machinery to reduce operating expenses while supporting compliance with environmental standards.
- Conduct thorough research on all available financing and acquisition options to determine the most viable and valuable approach for specific needs and projects.
Understanding the Construction Equipment Lifecycle
Every piece of equipment goes through different stages over its lifetime within a construction business. The first key step is evaluating options for acquiring the necessary machinery for upcoming projects.
This involves assessing initial costs, financing terms, tax advantages, and resale value to determine the most viable approach.
Acquisition Phase: Purchasing or Leasing Equipment
When starting or taking on large projects that require heavy machinery, construction companies must research their equipment needs thoroughly to identify the right options. This includes comparing the costs of purchasing versus leasing equipment.
Purchasing provides ownership but requires a higher upfront cost, while leasing offers lower monthly payments and flexibility to update the latest technology. Both choices must be sifted through based on factors like repayment terms, maintenance responsibilities, and project productivity enhancements.
Utilization Phase: Maximizing Equipment Productivity
Once acquired, the focus shifts to fully utilizing equipment capacity on construction projects. This involves thorough planning and logistical coordination to minimize delays. Proper operator training also helps extract the highest productivity levels while keeping operating costs as low as possible.
Maintenance Phase: Ensuring Longevity and Efficiency
Regular maintenance per manufacturer guidelines is key to equipment dependability over the long run. This includes scheduled services as well as repairs during unexpected breakdowns.
Tracking maintenance and repair costs allows for accurate budget forecasting. It also ensures equipment continues meeting requirements efficiently with minimal financial burden.
Replacement Phase: Upgrading or Disposing of Equipment
As equipment ages, construction businesses must evaluate replacement options based on changing needs and technology advancements.
This involves assessing resale value, repair costs, efficiency gains, and financing capabilities to determine if upgrades or new purchases are more cost-effective in the long run compared to continued maintenance of older machinery.
Factors Affecting Long-Term Investment Decisions
Making informed long-term investment choices regarding construction equipment requires evaluating multiple considerations. Key among these is thoroughly understanding project needs and financial capabilities to select options providing the best value over extended periods.
Equipment Selection: Choosing the Right Machinery for the Job
- Specific machinery requirements: Evaluate equipment specifications to ensure models meet project scope and tasks.
- Maintenance and repair costs: Factor in the total cost of ownership, including scheduled servicing and unexpected breakdown repairs.
- Operational expenses: Compare operating costs of different equipment types, including fuel consumption and labor requirements.
- Productivity enhancements: Consider efficiency gains that specific machinery provides to maximize output while minimizing delays.
- Technological advancements: Research the latest innovations to identify features improving functionality for future needs.
- Resale and replacement value: Analyze the equipment’s potential residual worth or trade-in allowance over the ownership period.
Total Cost of Ownership: Evaluating Initial and Operating Costs
Proper evaluation of a piece of equipment’s total cost of ownership over its projected lifespan is essential for making cost-effective decisions. This involves comprehensive market research to compare initial purchase or lease prices against ongoing expenses like maintenance, repairs, fuel, and personnel.
Only by accounting for all direct and indirect costs can construction businesses optimize long-term investment in machinery.
Technology Integration
Advanced technologies integrated into new construction equipment models provide opportunities to enhance productivity, reduce costs, and streamline operations. However, their impact must be thoroughly assessed.
Factors to research include efficiency gains that can save fuel and labor, connectivity features enabling remote monitoring to optimize maintenance and repair scheduling, and sensors assisting with precision tasks. It’s also important to understand the additional upfront and ongoing expenses advanced technologies require compared to conventional options.
Regulatory Compliance
Ensuring purchased or leased equipment adheres to applicable industry regulations and standards is a key consideration in long-term investment planning. Construction projects often have specific compliance requirements regarding machinery safety features, emissions levels, and operational certifications.
Non-compliance can result in expensive repairs, penalties, or project delays. Thorough research of regional regulatory guidelines is necessary when selecting models.
This involves examining factors like certification requirements for new versus used equipment, maintenance schedules needed to retain compliance over the ownership period, and upgrades expected to future-proof investments against changing regulations.
Comprehensively accounting for compliance costs at acquisition and over the equipment’s lifespan helps make informed choices aligned with the construction industry’s evolving needs.
Financial Analysis and Cost Benefit Evaluations
Making equipment investment choices requires a thorough financial analysis of long-term costs and benefits to identify the most viable options aligned with a construction business’ capabilities.
Net Present Value (NPV) Analysis
Net Present Value analysis allows businesses to evaluate equipment investment projects by discounting all expected cash flows to current dollars using a discount rate. This provides visibility into a project’s profitability over its projected lifespan by accounting for the time value of money.
Construction firms can use NPV when comparing purchasing, leasing, or rental options to understand how costs and benefits compare between alternatives under varied conditions and inflation scenarios.
Factors like initial costs, tax implications, maintenance schedules, resale value, and financing terms are incorporated to determine the most cost-effective solution.
Internal Rate of Return (IRR) Analysis
- The internal rate of return analysis determines the efficiency of an equipment investment by identifying the rate of return that makes the net present value of the project cash flows equal to zero. It helps construction businesses establish the minimum acceptable rate of return for a potential project.
- The IRR is then compared to the cost of capital or required rate of return threshold set by the company. Projects with an IRR exceeding this rate are deemed financially worthwhile.
- This technique evaluates the feasibility of multiple investment alternatives by comparing the unique IRR of each option.
- It incorporates the concept of the time value of money to discount future cash flows at the IRR discount rate to account for risk and uncertainty over the project’s lifespan.
- By outlining realistic cash inflows and outflows under different economic conditions and equipment performance scenarios, IRR analysis helps determine a project’s ability to provide the target rate of return.
- It allows construction firms to make informed choices by identifying the selection with the highest IRR above the cost of capital benchmark.
Payback Period Analysis
The payback period is required for a project’s cumulative cash inflows to recover the initial cash outflow. Construction companies commonly use this metric to assess potential equipment investment liquidity and risk level.
It also helps evaluate options requiring relatively lower upfront costs. Factors like tax implications, expected inflation over the payback term, and cash flow patterns are incorporated to compare alternatives’ payback periods accurately.
Life Cycle Cost Analysis
- Life cycle cost analysis considers all anticipated expenses associated with owning, operating, and maintaining a piece of equipment over its projected useful life.
- It factors in scheduled service, repair, and maintenance costs outlined by manufacturers to provide visibility into the total financial commitment for each year.
- The resale or residual value of the equipment is also accounted for to determine its salvage benefits at the end of the analysis period.
- This technique allows construction firms to compare the total costs of various equipment options to identify the most cost-effective long-term solution.
- It helps optimize long-term investment planning for equipment by outlining overall financial implications over the asset’s full life cycle.
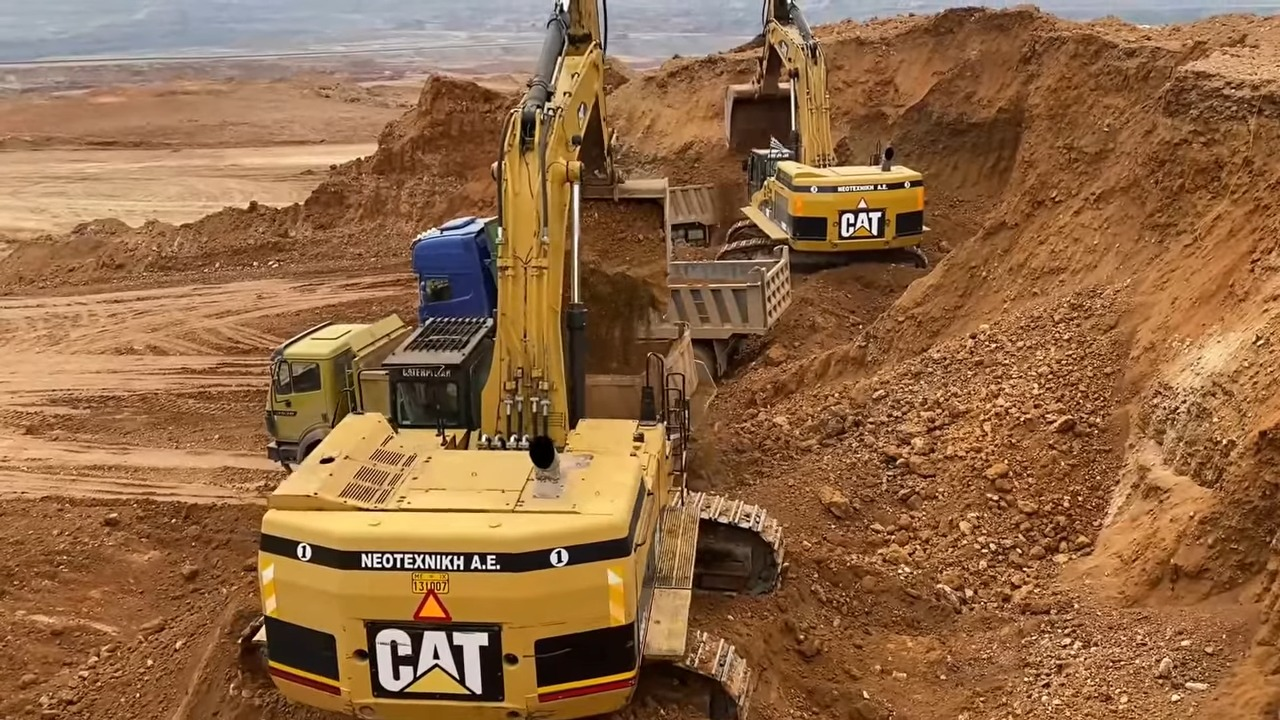
Risk Assessment and Mitigation Strategies
Proper evaluation of potential risks helps construction firms make well-informed long-term investment decisions regarding equipment.
Identifying Risks in Equipment Investment
Thorough market research and financial analysis are necessary to identify key risks associated with equipment investment decisions, such as changes in interest rates impacting financing costs, fluctuations in resale value over the ownership period, unexpected repair requirements, and new technological innovations affecting productivity.
This involves factoring in macroeconomic conditions and industry forces that can introduce uncertainties.
Strategies for Mitigating Risks and Uncertainties
Diversifying the mix of owned, leased, and rental equipment enables businesses to manage cash flows better and meet the fluctuating resource demands of projects. Opting for flexible financing options that allow refinancing or upgrades and comprehensive maintenance agreements limiting repair expenses can also help address risks.
Entering equipment-sharing agreements during low-demand periods and maintaining adequate contingency funds for unexpected repairs or replacements further mitigate uncertainties in long-term investment planning for construction needs.
Sustainable Practices and Environmental Impact
As the construction industry continues to evolve, embracing sustainable practices can benefit equipment investment decisions both environmentally and financially over the long run.
Embracing Sustainable Equipment Practices
Selecting machinery certified for lower emissions, fuel efficiency, and use of renewable energy supports compliance with evolving industry regulations while reducing operational costs through lower fuel and maintenance requirements.
Opting for electric models or those integrated with advanced technologies like telematics also helps minimize environmental footprint through remote monitoring that enhances productivity and lowers repair turnaround times.
Environmental Impact of Construction Equipment
Thoroughly researching equipment specifications regarding emissions and assessing the total cost of ownership aids in identifying options for minimizing environmental impact through lower greenhouse gas production and overall reduced resource consumption over the lifespan.
This involves factoring in fuel usage projections and maintenance schedules, ensuring adherence to compliance standards. Comparing machinery based on sustainability metrics allows for informed choices aligned with the industry’s focus on reducing carbon footprint through optimized long-term investment in equipment.
Future Trends and Industry Outlook
Keeping abreast of emerging trends enables construction firms to strategize equipment investment aligned with the industry’s evolving landscape.
Technological Advancements in Construction Equipment
Ongoing research and development yield new machinery integrated with automation, robotics, the Internet of Things (IoT), and telematics.
These innovations enhance productivity, reduce environmental impact through lower emissions and fuel usage, improve worker safety, and minimize operational expenses by optimizing maintenance schedules.
Thoroughly assessing such advancements allows businesses to future-proof long-term investments and maximize returns over extended periods.
Impact of Market Trends on Long-Term Investment Planning
Careful analysis of demand drivers, regulatory changes, sustainability priorities, and competitive conditions aids strategic decision-making. Monitoring consolidation trends within the rental, leasing, and financing sectors further helps identify optimal sources for acquired or leased equipment.
Adapting investment strategies aligned with evolving opportunities and challenges like expanded infrastructure spending, skilled labor shortages, or tariff implications ensures continued alignment with the industry’s direction.