What Are Construction Air Compressors and How Are They Used?
Meta Description: Learn about the various types of air compressors used in construction, their applications in projects like drilling, lifting, and tunneling, and factors to consider when choosing one for your needs.
This article provides an overview of air compressors used in the construction industry. It discusses the types of compressors suitable for construction needs and how compressed air powers important tools on work sites.
Key factors to consider when choosing a compressor are also highlighted. The aim is to help construction contractors select the right compressor that meets their air supply quality demands while remaining cost-effective and reliable.
Key Takeaways
- Air compressors are used to power pneumatic tools for drilling, hammering, and lifting equipment through compressed air.
- Depending on the power needs, different sizes and types of air compressors are suited for industrial, commercial, and consumer applications.
- Towable compressors are portable and ideal for construction sites to power tools as needed without being tied to utilities.
What is an Air Compressor?
An air compressor is a vital equipment or process that compresses air using an electric motor or engine. It provides compressed air, which is used to power or drive pneumatic tools and equipment across various industries.
How Does An Air Compressor Work?
- An air compressor uses an electric motor or engine to turn a shaft connected to a piston or screw-type compressor. As the shaft rotates, it pushes the piston or screw, which compresses incoming air into a storage tank.
- The incoming air first enters an air intake filter, removing dirt or debris. It then travels into the compressor body, where it is compressed. As the piston or screw moves, it reduces the volume of air but increases the pressure.
- The compressed air is then stored in a storage tank at high pressure, usually between 75-150 pounds per square inch (psi). Access ports on the tank allow the compressed air to be distributed to pneumatic tools and equipment attached to the compressor via air hoses.
- When a tool is turned on, it opens a valve that releases the compressed air from the tank through the hose and into the tool. The air powers the internal mechanism that drives the tool. As the tool is in operation, it consumes the compressed air until the job is completed or the tank needs to be refilled.
- The air compressor automatically switches on via a pressure switch when the tank pressure drops and runs through the compression cycle to refill the storage tank. This ensures a continuous supply of compressed air is available on demand for powering portable air tools.
Types of Air Compressors Used in Construction
Several air compressors are commonly used in construction sites to power pneumatic tools and equipment efficiently. The right choice of compressor depends on the specific needs of the various job sites. Portable and towable compressors are especially popular in construction due to their mobility and ease of transportation between work locations.
Portable Air Compressors
Small and lightweight portable compressors are highly maneuverable, making them well-suited for jobs that require carrying the compressor to restricted or hard-to-access areas. Their compact size allows portable compressors to be easily loaded into delivery vans or pickup trucks for transportation between various construction areas.
Some portable compressors even have removable fuel tanks for enhanced portability. This mobility enables workers to take compressed air on busy construction job sites.
Towable Air Compressors
Towable compressors are another convenient option for construction sites. They are compact enough to be pulled by vehicles yet have enough size and stability to handle rough or uneven terrain commonly found in construction sites and areas.
Towable compressors are designed for jobs that require moving the compressor around, such as restoration work involving multiple locations. Their trailer setup allows towing the compressor between work sites while providing powerful air delivery.
Heavy Duty Air Compressors
Heavy-duty stationary compressors are suitable for the most demanding construction applications like road building and civil engineering projects that involve earthmoving. They are robust and weather-resistant, with high-performance capabilities to continuously run pneumatic tools and equipment in tough outdoor conditions.
Stationary compressors deliver reliable compressed air supply for large-scale jobs where mobility is less important than output and durability.
Choosing the Right Air Compressor for Construction Needs
When choosing an air compressor while working in construction, choosing the appropriate one is essential for maximizing efficiency on job sites. A compressor not meeting power or mobility needs can seriously hinder productivity. Contractors must carefully evaluate their tool requirements and environmental factors to select a machine suitable for reliable, versatile use.
CFM Requirements
One of the most important specifications is the compressor’s CFM rating. CFM refers to the cubic feet per minute output of compressed air, representing the unit’s power capacity. All pneumatic tools require a minimum CFM to function properly.
Evaluating one’s existing equipment and planned purchases allows selecting a compressor to handle present and future demands. Opting for a model that exceeds needs provides flexibility for taking on a wider scope range of projects over time.
Power Source Options
Another key decision is the compressor’s fuel type or electricity requirements. Portable gas-powered units offer mobility but come with refueling needs. Electric models are convenient for enclosed areas yet depend on available power sources on site.
Diesel operation provides fuel independence yet comes at higher initial and fuel costs. Towable air compressors to power and can access remote locations while avoiding fuel transportation. The most suitable power source depends on tasks, locations, and budget.
Size and Mobility Factors
For construction, compressors must allow working in various areas with ease. Smaller portable units are suitable for lifting and accommodating work in difficult spaces but lack power for heavy-duty use.
Larger stationary compressors prove ideal for main work areas but pose issues on multi-level projects. Towable compressors offer a balance of capacity and transportability. The most practical size comes down to the compressor’s intended uses and how easily it can be relocated as needs change.
Noise Level Considerations
In some environments, minimizing noise is also a factor. Residential projects may require keeping the disturbance low. Quieter compressors prevent disrupting other tasks and avoid issues with noise ordinances. However, more sound-insulated units tend to be less portable. The right balance relies on assessing location sensitivities and prioritizing either mobility or quiet operation based on specific needs.
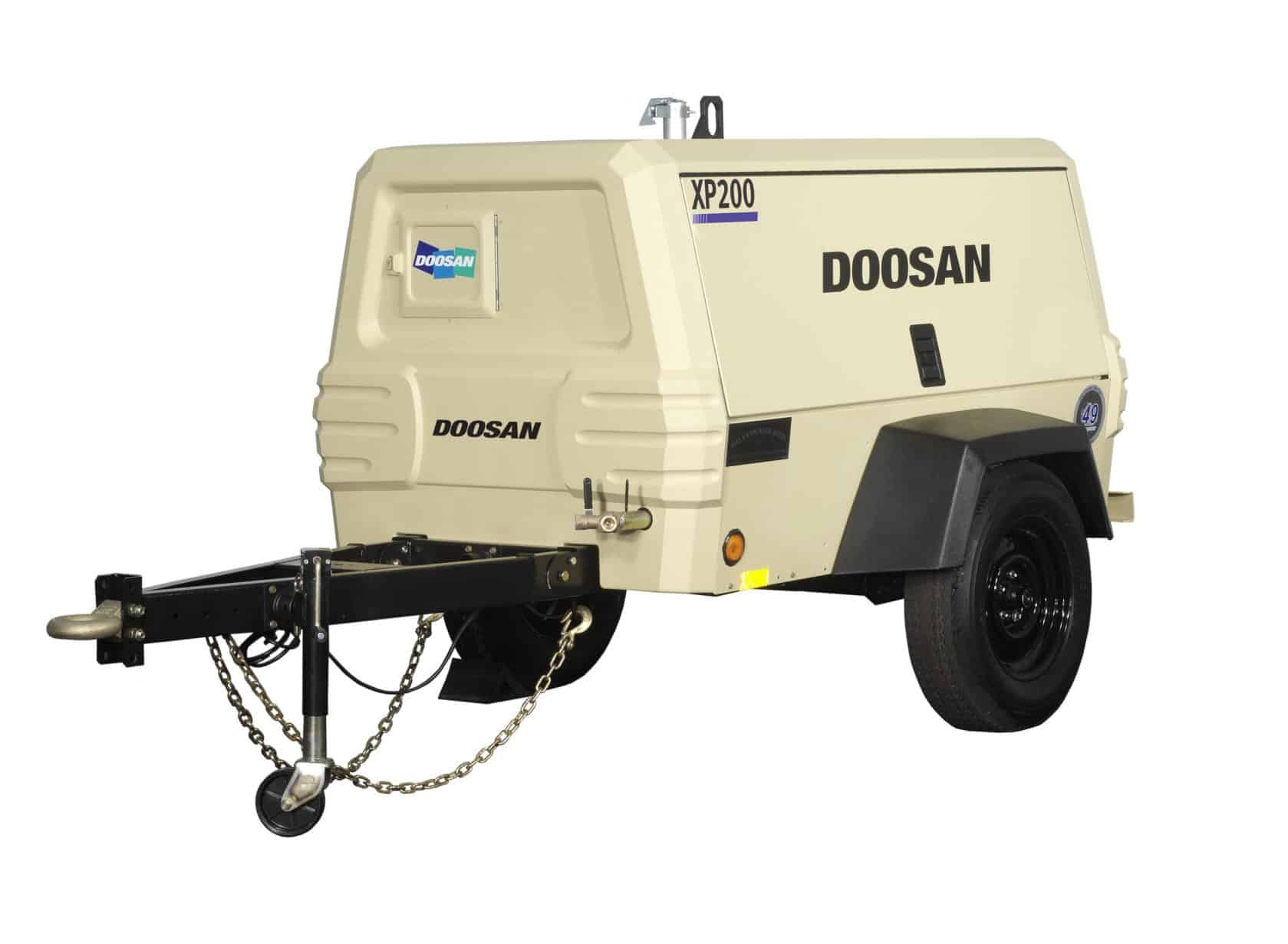
Common Uses of Air Compressors in Construction
The construction industry relies heavily on compressed and small air compressors for various applications. Air compressors provide a consistent supply of compressed air that can power numerous pneumatic tools safely and efficiently. Some of the most important uses of compressed air on construction sites include powering pneumatic tools, material handling equipment, and various digging and groundwork operations.
Powering Pneumatic Tools
One of the primary uses of compressed air in construction is to power pneumatic tools. These air-powered tools, also known as air tools, are very useful for drilling, hammering, sawing, and grinding. They are lighter than electric tools and have fewer moving parts, making them easier to use and maintain.
Air tools are also considered safer to operate as there is no risk of electric shock. Common air tools used on construction sites include jackhammers, drills, impact wrenches, grinders, sanders, and nail guns. A portable air compressor ensures a continuous supply of compressed air is available to power these pneumatic tools as needed.
Material Handling Equipment
Material handling equipment requiring compressed air is widely used on construction sites for lifting and lowering materials. Equipment such as hoists and lifting devices use compressed air to function reliably and safely handle loads.
Air-powered hoists help lift heavy construction materials like bricks, steel beams, and concrete panels into place quickly and precisely. Towable compressors are convenient for powering pneumatic equipment and machinery on job sites.
Digging and Groundwork Operations
Construction projects involve extensive digging and groundwork that can be completed more efficiently using compressed air. Road cleaning, digging trenches and tunnels, and cutting or breaking surfaces rely on compressed air. Air tools like jackhammers, drills, and saws use compressed air to efficiently dig through tough surfaces like rocks and pavement.
Road cleaning machines also use compressed air to power their systems to keep surfaces clean. When digging underground tunnels, controlled compressed air is used to balance the hydrostatic pressure of the surrounding earth. Portable air compressors can provide the mobile supply of compressed air needed for pneumatic digging and ground groundwork equipment on job sites.